Fahrzeugfedern – eine ganze Wissenschaft, die auf drei Säulen basiert
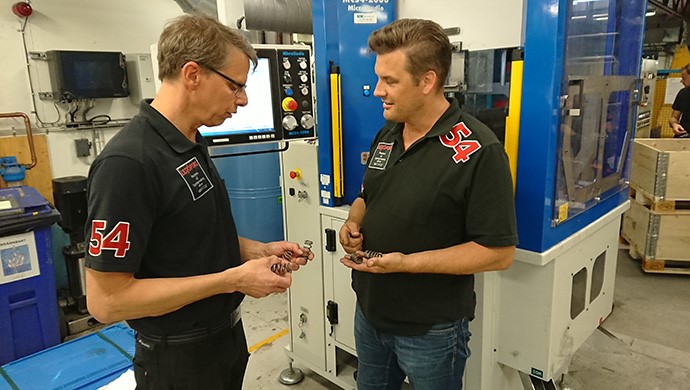
Materialien. Herstellungsprozess. Konstruktion. Das Zusammenspiel dieser drei Faktoren ist entscheidend für die Eigenschaften einer Feder. Da auf diesem Gebiet in Schweden nicht geforscht wird, entwickelt Lesjöfors das Know-how, das zur Herstellung von auf härteste Beanspruchungen ausgelegten Fahrzeugfedern, selbst.
Bei Lesjöfors Industrifjädrar im schwedischen Hudene werden u. a. Spezialfedern für tiefergelegte Motoren hergestellt. Öhlins Racing ist ein bekannter Kunde, den Lesjöfors seit über 20 Jahren mit Federn für Stoßdämpfer beliefert. Bei einem Kundenstamm, der in puncto Toleranzen, Oberflächenbehandlung und Leistung höchste Anforderungen an die Federn stellt, ist es entscheidend, immer einen Schritt voraus zu sein, um die Position des Unternehmens behaupten und weiterentwickeln zu können. Stefan Musslinder ist technischer Leiter des Lesjöforskonzerns. Er erklärt die Voraussetzungen, die erfüllt sein müssen, um in der Branche erfolgreich zu sein.
„Die Eigenschaften einer Feder basieren auf drei Faktoren: Materialien, Herstellungsprozess und Konstruktion. Durch weitreichende Kompetenz in allen drei Bereichen können wir die Vorgaben erfüllen, die wir von den Kunden erhalten.“
Die Funktion bestimmt das Design und das Material
Die Materialeigenschaften zu kennen und davon ausgehend die Drahtdurchmesser und die Anzahl der Wickelungen zu berechnen, ist für eine optimale Feder unerlässlich. Für verschiedene Einsatzbereiche stehen eine Vielzahl von Materialien zur Auswahl. Federstähle gehören zu den härtesten Stahlsorten. Dies ist eine Voraussetzung, um den enormen mechanischen Spannungen standzuhalten, die an Federn in einem Fahrzeug entstehen. Die ständig steigenden Anforderungen im Hinblick auf geringes Gewicht und geringe Einbaumaße führen dazu, dass die Federn höheren Spannungen standhalten müssen.
Prozesse, um Festigkeit zu erreichen
Der Herstellungsprozess ist mindestens ebenso wichtig wie das Material, da die Eigenschaften durch verschiedene Behandlungen genau an den jeweiligen Bedarf angepasst werden. Nach dem Wickeln werden die Federn abhängig von der Materialsorte und der Art der Federanwendung bei 200–450 °C wärmebehandelt. Bei dieser sogenannten Spannungstemperierung lösen sich die inneren Spannungen der Wicklung. Anschließend werden die Federn in allen Fällen, in denen die Endflächen flach sein sollen, geschliffen. Schleifen ist eigentlich eine Grundvoraussetzung für alle Druckfedern. Bei einfacheren Federanwendungen wird hierauf jedoch aus Kostengründen manchmal verzichtet.
Damit Federn – beispielsweise Ventilfedern in einem Verbrennungsmotor – während ihrer Lebensdauer einer großen Zahl von Belastungswechseln standhalten, ist Kugelstrahlen ein wichtiges, kritisches Verfahren. Indem kleine, harte Stahlkugeln gegen die Oberfläche geschleudert werden, werden Druckspannungen in die Oberflächenschicht des Materials eingebracht. Kugelstrahlen kann die Ermüdungsfestigkeit bis auf das 50-fache erhöhen.
Entwicklung von Berechnungsmodellen
Der letzte Schritt – vor der Oberflächenbehandlung, Kennzeichnung usw. – ist das Setzen, bei dem die Feder zwei- bis dreimal maximal zusammengedrückt wird, damit sie sich setzt. Hierdurch werden innere Spannungen im Material erzeugt, die den Belastungsspannungen, denen die Feder während der Anwendung ausgesetzt ist, entgegengesetzt sind. „Da die Feder beim Setzen kürzer wird, muss der Entwickler die Länge bei der Wicklung berechnen können.
„Das Berechnungsmodell mussten wir selbst entwickeln, da der Federbereich bisher im Prinzip ein weißer Fleck in der wissenschaftlichen Forschung ist. Um die optimalen Federn herstellen zu können, müssen wir die Technologie, die wir benötigen, weiterentwickeln. Nur so können wir Marktführer sein“, erklärt Stefan Musslinder.
Enorme Belastungen für Ventilfedern
Für besonders beanspruchte Ventilfedern, die, etwa bei tiefergelegten Motoren, extremen Belastungen ausgesetzt werden, sind in manchen Fällen weitere Maßnahmen erforderlich, um die entsprechende Festigkeit zu erreichen. Hier wird häufig mit Federsätzen gearbeitet, bei denen zwei oder drei Ventilfedern konzentrisch ineinander montiert werden. Hierdurch verringert sich die Belastung auf die einzelne Feder. Eine hervorragende Lösung für die begrenzte Fläche in dem Bereich, in dem die Feder arbeiten soll.
„Die Anforderungen sind in jeder Hinsicht hoch: Von den Prozessen zur Stahlreinigung über die Oberflächenbehandlung und Temperierung bis hin zum Schleifen und Kugelstrahlen. Anschließend findet das Setzen unter Wärmeeinwirkung statt, damit die Federn den hohen Temperaturen in den Umgebungen standzuhalten, in denen sie anschließend eingesetzt werden“, so Stefan Musslinder abschließend.
Wolfgang Hellman
Vice President Sales Germany
wolfgang.hellman@lesjoforsab.com
+49 (0)151 67875076
Tags: