Integrated Drive Systems – the Holy Grail for Industry?
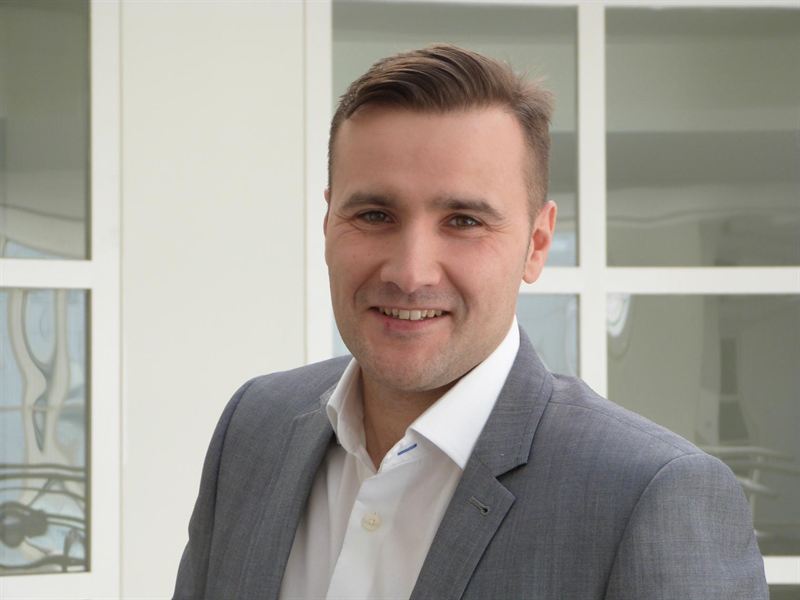
- John Inskip of Siemens Industry looks at how completely integrated drive trains can provide a successful solution
As the world economy slowly starts to recover, industry is investigating and implementing methods and technology to ensure long-term profitability and reliability.
In today’s economy more emphasis is being placed on the old adage of ‘getting more for less‘; in simple terms, optimising your business to return more profit. As responsible global citizens, companies are also looking at technologies to reduce their carbon emissions and utilise their energy consumption more wisely.
Industry in particular is looking at further issues such as lifecycle management, global support and vendors who can provide a single source of supply, to maximise productivity.
How can these issues be addressed? How can a simplification of equipment be standardised yet still meet the holistic needs and applications of individual customers? How can ‘getting more for less‘ be realised?
Trying to address these issues purely by using clever technology will only achieve benefits to a certain degree. To be able to gain the most benefit, businesses must look beyond just ‘a clever box‘ to see how their business needs can be addressed, now and in the future.
Integrated drive technology – what is it?
Within industry, regardless of type, all drives utilise electric motors. A large proportion of them are controlled by variable speed drives connected to gearboxes and couplings.
This equipment may have been sourced from various suppliers and quite possibly has been installed to help address some of the issues mentioned above. Now, let’s explain integrated drive technology.
The integrated drive system (IDS) is a concept which elevates products beyond pure product supply. It is an all-encompassing solution, whereby the ‘complete drive system solution‘ is specified and supported throughout its lifecycle.
It is a method of addressing both the operational and energy efficiency requirement of a company. It optimises a drive system to the highest degree of performance and allows complete acquisition of data to achieve predictive maintenance, ie to see and solve problems before they occur and create downtime.
The system supports the machine or plant throughout its entire lifecycle. It simplifies procurement of equipment by using a single source supply route. The key word used throughout is optimisation.
The concept of IDS starts with procurement
Procurement can be difficult and a time-consuming task; several vendors may be involved. This can make your business and procurement requirements harder to understand, leadng to a non-aligned solution. A non-aligned solution has the potential to be misunderstood and so may not meet all your business and technical needs (Fig.1).
Fig.1 Comparison of single-source and multi-source supply
Alternatively, adopting a single source supplier can align your needs and business requirements to another single business, allowing for a single point of contact for all equipment to be supplied. An experienced supplier offers significant value added services such as expert engineering support, unparalleled experience in your sector and production facilities around the world and close to you.
The design stage – encompassing IDS
Having the correct tools to be able to design, simulate and justify cost savings and performance are key to being able to realise the full potential of any industrial machinery package. The implementation of IDS allows the user to implement software that can both specify, simulate and calculate energy efficiency and performance of the drive system. This is critical to ensuring the specific requirements of a user’s application.
Commissioning with IDS
To ensure ease of commissioning and the construction of the drive system, IDS solutions have a seamless approach and harmonisation of the drive train components, ensuring there is no risk of incompatibility between them – and ensuring commissioning time is kept to a minimum (Fig.2).
Fig.2 Drive train component integration
Integration of the drive system to the machine control system and beyond can be achieved using the latest communication protocols, allowing for increased availability, data access, flexibility and remote diagnostics, and ensuring the maximum potential is achieved (Fig.3).
Fig.3 Machine control system integration
Operational performance
In order to confirm that a machine or drive system is always working at peak performance, IDS involves using lifecycle support, a method of maintaining the drive system in a planned manner. This avoids unnecessary failures, and ensures that both the performance and efficiency of the drive train are not compromised.
Getting the best operational performance requires measurement or data acquisition, the practice of continuously monitoring a plant or system to achieve the highest level of quality and performance. This means that profitability and machine utilisation are maximsed – as well as preventing unforeseen breakdowns.
For future proofing the solution, lifecycle support can also take the responsibility of modernisation programmes or modifications so that industry’s constantly changing demands are always met and exceeded.
In summary
Integrated drive systems are methods of business being able to address the forever changing industrial environment; they are a means of ensuring that all of business’s technical, procurement, energy and operational needs are met.
Fully integrated drive systems like this one bring significant benefits to everyone
IDS solutions benefit the end user, equipment manufacturer and the systems/solutions integrator alike, and guarantee the availability, performance and longevity of the plant and machinery.
John Inskip is Product Manager at Siemens Industry (Drives & Motion Control).
PHOTO-CAPTION: John Inskip of Siemens Industry
Contact for journalists:
Bridget Summers
01723 447424
For further information, please see www.siemens.co.uk/automation
Siemens in the UK
Siemens was established in the United Kingdom 170 years ago and now employs around 13,760 people in the UK. Last year’s revenues were £3.36 billion*. As the world’s largest engineering company, Siemens provides innovative solutions to help tackle the world’s major challenges, across the key sectors of energy, industry, infrastructure & cities and healthcare. Siemens has offices and factories throughout the UK, with its headquarters in Frimley, Surrey. The company’s global headquarters is in Munich, Germany. For more information, visit www.siemens.co.uk
* Data includes intercompany revenue. Data may not be comparable with revenue reported in annual or interim reports.
The Siemens Industry Sector (Erlangen, Germany) is the world’s leading supplier of innovative and environmentally friendly products and solutions for industrial customers. With end-to-end automation technology and industrial software, solid vertical-market expertise, and technology-based services, the Sector enhances its customers’ productivity, efficiency and flexibility. With a global workforce of more than 100,000 employees, the Industry Sector comprises the Divisions Industry Automation, Drive Technologies and Customer Services, as well as the Business Unit Metals Technologies.
Tags: