A cut above the average
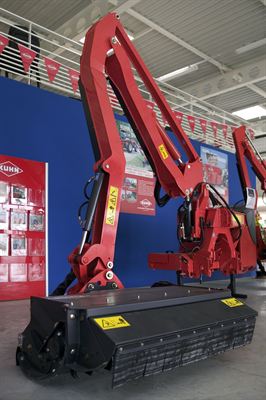
A new, more convenient and ergonomic grass mower unit for tractor mounting has been developed by the French company Kuhn. The Pro-Longer unit is made of advanced high strength steel, which has paved the way to major improvements. The designers have cut its weight, increased the strength and reduced the number of parts. The result to the customer is better operating economy and a safer working environment. The unit was awarded with the Swedish Steel Prize 2008.
In launching the work on the new unit, Kuhn aimed at reaching new target groups. The company had so far produced equipment mainly for agriculture. But the aim now was to broaden the operations and also become a supplier to road maintenance contractors, public authorities
and similar groups.
”Our task was to develop a machine for demanding professional use, in which strict demands are made on strength and a long useful life,” says Mickaël Peterschmitt, Project Leader for the development work at Kuhn. ”There is a great difference between a machine for agricultural work, which may perhaps be in use for 100 or 200 hours a year, and a machine such as the Pro-Longer designed for operating 1500 hours a year. So we had to redevelop our existing machine, since it was built of traditional structural steel.”
High stresses
A tractor-mounted mower unit is subjected to very high stresses. The mower unit is mounted at the extremity of a rotatable arm. The arm can be turned in different directions so that the driver can access virtually anywhere. At the same time, it must be possible to angle the unit to cover a maximum area. Considering that the ground on which the tractor runs is generally uneven and sloping, the torsional forces are very high. To counteract these forces, a large and heavy counterweight is mounted at the rear of the tractor. The weight of the unit is decisive to the wear sustained.
It was therefore important for the designers at Kuhn to minimize the weight without compromising on strength.
”We quickly realized that it was equally important to reduce the total weight as it was to produce a strong design,” explains Pascal Gauthron, Project Engineer at Kuhn, who also bore main responsibility for the design of the Pro-Longer. ”The solution was to use advanced high strength steel. This enabled both objectives to be achieved.”
Improved ergonomics for the driver
Consideration was also given to how production could be arranged in an efficient manner. One of the requirements was to automate the production process, using equipment such as welding robots. The driver’s working environment was also an important factor. The aim was to locate the unit arm as far forward on the vehicle as possible, so that the driver would have a good overview of the mowing work – and be able to stop quickly if anything should go wrong.
The choice fell on a combination of hot-rolled, advanced high strength steel with a minimum yield strength of 700 MPa, and heavier high strength structural steel with the same strength. This enabled the weight of the main arm to be cut by 23 percent, which also allowed for a lighter counterweight to be used. In spite of the reduced weight, the strength of the arm was increased by 20 percent. The result of the lower weight is a reduced load on the tractor, less wear of the chassis and wheel suspensions, and smoother running.
Simpler production
In the design work, Kuhn has modified the design of the arm beams. In the past, square-section beams were used, with welded mountings and reinforcements for fitting the hydraulics and pivots. In the Pro-Longer, the arm consists of four parts that are welded together. The welds are located on the top and underside of the arm instead of the sides where the load is highest. This design has yielded much higher torsional stiffness. The mountings and reinforcements are fully integrated into the arm, which has radically reduced the number of component parts. This has resulted in simpler and more cost-effective production.
The development work on the Pro-Longer has been successful. Almost 200 units are now in operation in France, Germany, Great Britain and Denmark, and the units have lived up to expectations. The market appears to like what it has seen, and new customers are waiting in line. At the Kuhn plant outside Nantes in western France, production is in full swing. The plant is one of five Kuhn factories. There are a further two in France, and the others are in the USA and Brazil.
Picture: Kuhn was awarded with the Swedish Steel Prize 2008 for the Pro-Longer.
Text and digital picture can be downloaded from www.swedishsteel.co.uk
For further information, visit:
www.steelprize.com
www.ssabtunnplat.com.