Swedish innovativeness behind a new concept for product development
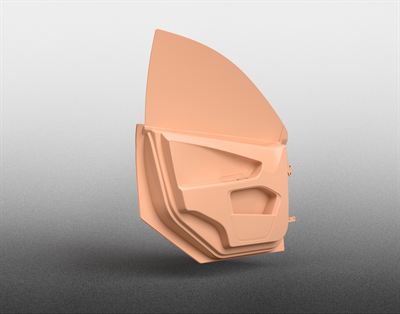
The Swedish lightweight project SåNätt is an interesting example of new forms of cooperation and innovation between suppliers, academic institutions and OEMs. A freethinking approach like that used in the aviation industry has created weight-reducing (WRED) solutions which led to a combined weight reduction of 43 percent on a car corresponding to a Volvo S60.
Some of the R&D results of the SåNätt project will be presented at the Swedish joint stand of the Scandinavian Automotive Supplier Association (FKG) during the IAA.
The project is a clear example of how more and more development work will be done at the supplier stage. The European industry association Clepa has even stated that by 2020 two-thirds of automotive development costs will occur at the supplier stage. The SåNätt project does not contract this.
Using this approach, competent suppliers result in competent OEMs and vice versa. It is also worth mentioning that Sweden is the leading individual nation in the EU in terms of innovativeness, and according to the OECD also tops the list of the number of patents per capita.
SåNätt is the result of two and a half years of R&D work by 30 suppliers to the automotive industry, Volvo Cars, FKG, six institutes of higher learning, and Innovatum – a science centre in Trollhättan.
“Actually, the unique aspect of the WRED project was not that we succeeded in producing a good concrete result in the form of various subsystems, but rather that so many participants were able to work together in a totally new way,” comments Peter Bryntesson, project coordinator from the FKG.
Chalmers University of Technology in Gothenburg contributed the successful development methodology, which is similar to the aviation industry’s development process. The approach is unique in that it does not resemble the automotive industry’s usual method – that the end result must fit into the existing production facilities. Instead, the method breaks with well-worn conventions – it goes outside the usual “box”.
“In this way we succeeded in developing the car’s various systems faster and better than usual, and even achieved a higher target than the original one,” Bryntesson says.
The project focused on functions and properties of importance to the end customer. These were broken down into smaller parts and weighted relative to each other: property to property, function to property, function to function. The team then tried to create new components and systems which each fulfilled several functions. For example, one leaf spring was created to replace four chassis components: the subframe, control arm, spring and anti-roll bar. In this way several expensive components could be replaced with just one, saving weight and money.
The SåNätt project is one of the exhibitors at the Scandinavian stand being organised by FKG at the IAA in Hannover from 24 September to 2 October.
Footnote: The developed subsystems did not undergo all tests because they were part of a research project but the most important tests were done and the results were as good as or better than those for the reference car.
FKG - Fordonskomponentgruppen
CEO: Fredrik Sidahl
fredrik.sidahl@fkg.se
+46 706 80 59 53
www.fkg.se
Facts: FKG – Fordonskomponentgruppen
FKG is the Scandinavian automotive supplier association. Member companies range from large, global so-called Tier 1-suppliers and medium-sized engineering companies to small start-ups, often build around innovation. FKG is situated on Gothenburg, Sweden and has 380 member companies.
Tags: