Self levelling – easy to imagine, hard to design
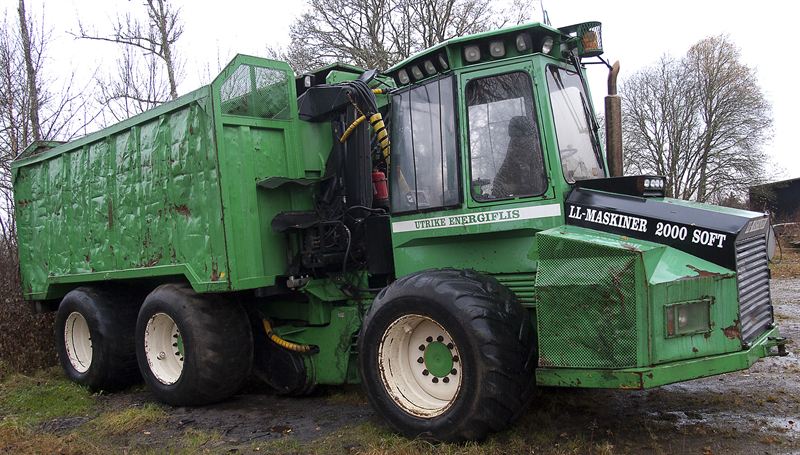
Focus: Innovators
Lars Lameksson has played an important role in the development of modern forestry machine systems. Several times his company LL Skogsmaskiner has reached the stage of being able to start mass production.
“But solving problems is what drives me, not managing factories,” he says.
LL Skogsmaskiner still exists and has been taken over by Lars’s sons although he remains actively involved. His workshop still stands where it all began, in the woods near the town of Ljungby in southern Sweden. Here he has designed and built a number of unique forest machines.
The best known of these is his harvester with pendulum arms. It first appeared in 1986 under the name Spindeln (The Spider) and is still in production under the EcoLog label. The machine’s design was pioneering and still holds its ground against the competition.
Pendulum arms and wheel hub motors
Like so much else in the development of forest technology, it all began with a request from a forest contractor. The single-grip harvester was becoming widespread and contractors wanted one that could also work in steep terrain. Lars knew that the harvester must be self levelling, that is, be able to keep itself horizontal even on a slope, so that the crane can retain the full force of its swing.
Other manufacturers had already tried pendulum arms. Lars realised that a good solution would be to combine pendulum arms with a technology that LL Skogsmaskiner had been the first to use on its Trollet forwarder, that is, fully hydraulic operation.
“We put a hydraulic motor in every wheel hub, which simplified the whole design of the machine,” he says. “The entire transmission could be replaced with hydraulic hoses.”
The real innovation
The idea was simple on paper but needed an innovation in order to be useful in practice. The ingenious solution involved connecting the hydraulic pistons of the pendulum arms with each other so that the machine automatically self levelled while it was in motion but the function was blocked while the machine was standing still. When the harvester was still it could lean 25 degrees to the side and 15 degrees forward or backward.
And with that, the harvester “ballet” performance that occurs at every Elmia Wood was born. Lars’s design was first taken over by the Swedish company Skogsjan, which then sold it on to Caterpillar. Today it is EcoLog that produces the “Spider’s” successors in five different versions. LL Skogsmaskiner now services the EcoLog machines, so Lars has been able to follow the technological advances at close quarters.
“The basic design is the same as the one we developed back in 1986,” he says.
When the first harvester equipped with pendulum arms was presented in 1986 it was received with a mixture of delight and dread. Everyone realised the advantages of having a self-levelling harvester but many also feared high maintenance costs and a lot of downtime.
The designer’s own dream
Yet the “Spider” had a far simpler design than other harvesters, with fewer articulated parts. More than 25 years of experience has proven that the machine is extremely stable and reliable in service.
Officially Lars is now retired but he still works as a problem solver for the family company. He has one dream left to realise:
“We’ve always solved our customers’ problems but I hope to be able to develop a machine based on my own ideas,” he says.
Captions
lameksson_1.jpg
“It began when a contractor ordered a single-grip harvester for steep terrain,” explains Lars Lameksson, who created the harvester with pendulum arms.
lameksson_2.jpg
The first sketch of a harvester with pendulum arms, the predecessor to today’s EcoLog.
lameksson_3.jpg
“The design is about the same as that of today’s harvester from EcoLog,” says designer Lars Lameksson, here in front of a machine that was built by LL Skogsmaskiner and sold under the Skogsjan brand.
lameksson_4.jpg
The innovation was not the pendulum arms but rather the automatic self-levelling system.
lameksson_5.jpg
“The design was simplified by using hydraulic hoses instead of having a transmission,” Lars Lameksson explains.
lameksson_6.jpg
One of seven forwarders with pendulum arms, this one rebuilt for handling wood chips.
Watch the film about Lars Lameksson!
Contact:
Torbjörn Johnsen, Business Area Manager, Elmia AB
torbjorn.johnsen@elmia.se
46 36 15 22 54
Veronika Albert, Press Service, Elmia AB
veronika.albert@elmia.se
46 36 15 22 34
Elmia Wood 5–8 June 2013
Meet forestry professionals from all the World. The basic concept behind Elmia’s forestry fairs is that machines and technology for modern forestry should be exhibited in their right environment – the forest. The fairs are active and feature demonstrations that reflect the forest practices normal to Scandinavia. Elmia Wood is the world’s largest forestry fair and is held every four years in the forests near Jönköping, Sweden. The next fair is 5–8 June 2013. www.elmiawood.com
Elmia’s forestry fairs
Elmia Wood 5–8 June 2013
SkogsElmia 4–6 June 2015
Elmia Wood 7–10 June 2017
Tags: