New Exmac Automation Palletisation System Delivers Flexibility for Retail Logistics Plant
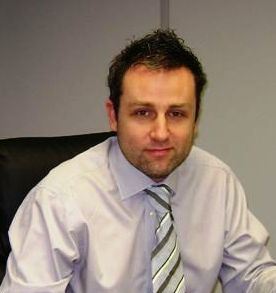
Gary Sweeney, managing director of leading conveying and materials handling specialist Exmac Automation explains how a recently completed upgrade of a palletising system for a major logistics company has significantly improved flexibility at a multiple packaging facility in Cambridgeshire.
Automating packaging processes that had been previously handled manually can create significant improvements in flow line efficiency while also reducing pack damage caused by manual handling, so when Exmac Automation was invited to tender for the upgrade of a busy packaging plant, the initial project review was vital in understanding and resolving its existing limitations.
The customer’s site receives cans and pouches of cat and dog food from a nearby processing plant, removes them from trays and, using a combination of manual and semi-automated systems, places them into packaging machines before they are shrink wrapped – typically into cases of four boxes. From this stage, three quarters of production had previously been manually palletised and the balance palletised using an existing robot. To aid rigidity when stacking, most pallets would then be fitted with cardboard corner boards held in place with masking tape applied by hand. Pallets were then transferred onto an automatic stretch wrapper by fork lift truck and transported to the dispatch yard.
Labour intensive hand-stacking and hand-packing at many stages meant that product and packaging could be accidentally damaged, so the main objective of the project review was to make the operation more cost-effective and create a ‘one-touch’ system that ensured pallets were manually handled as little as possible from production to distribution.
Also important was the need to integrate the new system with technology already on site, including an ABB robot and a conveying line, which rationalised equipment, controlled costs and avoided major staff re-training.
Exmac was one of a number of specialist companies invited to improve the efficiency of both the palletising and delivery-to-dispatch systems, by automating the existing process. The contract was awarded on a combination of cost, the fact that Exmac was UK-based, and that our logistics design team understood the customer’s objectives and introduced ideas that the customer hadn’t thought of!
Following a number of layout development phases focused on throughput, available space and, as always, financial considerations, the customer accepted a fully-automated Exmac system that integrated all palletising, corner board fitting, stretch wrapping and delivery-to-dispatch functions.
Our parent company MacDonald Humfrey Automation (MHA) provided the control systems, created complex software to integrate existing and new equipment, and developed universal software to manage the system’s diverse functions.
Product is now delivered in cartons where three lines feed into a new Exmac-designed and installed palletisation area comprising two robots (one existing, one new), conveyor systems – one we supplied plus one FOC from another customer site – the corner board machine and a shrink wrapping machine.
The Exmac materials handling solution featured one of our clutched UB500 case conveyor systems to collect product from the packing lines and deliver it, on three Exmac conveyor systems, into a twin-robot cell that was specifically designed to enable two robots to palletise the throughput from all three lines.
To insert pallets, two separate pallet destackers are installed, one for Chep pallets and one for Euro pallets. These automatically deliver pallets into each zone of the new robot cell and into the existing robot cell.
The robots use unique vacuum grippers able to handle cases in various arrangements to suit eight different layer patterns for both Euro and Chep pallets. This enables the customer to respond quickly to demands for any product. The gripper is also designed with a hinged side vacuum to collect loose trays that are fitted to certain products to prevent them slipping from the case assembly.
One customer had requested that after pouches are put into cartons and sealed, batches of eight cartons be loaded onto its own purpose designed trays. To accommodate this special requirement we sourced a new robot gripper design and re-programmed the software to enable it to introduce the special trays. Fortunately, through our relationship with MHA, we were able to deal with these additional changes efficiently, and the system is now fully integrated within the operation.
At the final palletising stage a cardboard layer pad has to be fitted between certain layers on each pallet. The layer pads are delivered into the robot cell on a trolley system, where outboard suction cups on the robots’ gripper pick a single pad and position it accurately onto the pallet stack. Full pallets leave the robot cells on a series of Exmac chain and roller conveyors and are fed onto the main outfeed line. At this point pallets are checked to confirm they are fully loaded and any ‘short’ pallets are automatically diverted to a secondary outfeed lane.
Next, we introduced a bar code reader to identify each pallet’s product type before transferring it by conveyor to a corner board fit machine. This receives information from the bar code reader, first to confirm whether or not the pallet requires corners and then to identify the size of pallet and type of corners required. If corners are to be fitted the pallet moves into the corner board machine and stops in its pre-determined position, where the corner boards are located and a banding tape fitted to secure them.
Pallets then leave the machine to await a routing decision on a turntable that will either deliver them into the existing stretch wrapper or re-route them onto a conveyor for delivery to a new stretch wrapper. As pallets leave the wrapper they are again identified by the bar code reader, this time to download data for a three-face label applicator, which prints and applies a unique label to three sides of each pallet, enabling retailers and large supermarket customers to identify the content. Pallets are then dispatched to an unload station.
The key to the success of the new palletisation area was identifying a significant problem with the previous layout during our project review. While the existing system automated the pouch lines it prevented the canned product line delivering pallets to the wrapper. We resolved this problem at the layout planning stage by developing an extension of the canned product conveyor line to merge with the pouch product conveyors before they reached the wrapping machines, enabling canned produce to also be automatically wrapped and labelled.
Ends
For further information contact:
Harry Chana, Exmac Automation, Unit 105 Pointon Way, Hampton Lovett, Droitwich Spa, Worcestershire, WR9 0LR
Tel: 01905 773851, Email: hchana@exmac.co.uk, Web: www.exmacautomation.co.uk
For press information contact:
Dennis Cantillion, Cantillion King Advertising 16 The Cornhill, Stroud, Gloucestershire, GL5 2JT
Tel: 01453 755551 Fax: 01453 751525 E-mail: dennis@cka.co.uk
About Exmac Automation:
Exmac Automation has years of experience in the design, manufacture, and installation of unit conveyors, conveyor systems and associated materials handling equipment for many industry sectors.
Part of the MacDonald Humfrey group of companies and with an annual turnover in excess of £16 million, Exmac Automation are market leaders in the supply of automated materials handling equipment to the automotive, aerospace, white goods, warehouse & distribution, nuclear, pharmaceutical and food & beverage industries.
Projects range from individual standard conveyors and bespoke handling applications, to complete turnkey contracts involving conceptual and process design, installation and commissioning.
Exmac Automation is ISO 9001 accredited and constantly strive to achieve continuous improvements in the overall quality of its products and service.
Tags: