Knowhow in production efficiency, line design and integration – FlexLink showcases capabilities at Pack Expo
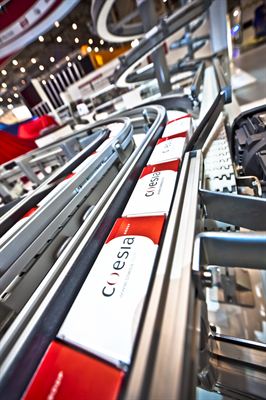
FlexLink will demonstrate the integration of continuous motion line balancing at Pack Expo, the leading North American packaging exhibition opening on November 2nd. Visitors will experience the latest developments in automated production flow solutions, including the new wide belt conveyor platform, designed for trouble-free operation. Factory and line designers will experience the FlexLink Design Tool, a state-of-the-art design tool with integrated simulation capability.
FlexLink, a leading provider of efficiency enhancing solutions, will deliver strong messages at PackExpo, from the easy and accurate design of packaging lines to solutions for high total efficiency.
Quality control and late stage customization in a flow
Together with ADMV, Hapa and Laetus, FlexLink will demonstrate the combined offer of the Coesia Industrial Process Solutions division. Inspection, print on demand and smart handling functions are connected in an intelligent flow and visitors will be able to order personalized items.
Products are controlled before and after the on-demand printing, safeguarding the quality of the correct print. In addition, the flow of products is balanced in different ways and the robot cell is placing the products in patterns. The line performance is continuously monitored by an application of FlexLink’s efficiency suite, Youtilize®.
High efficiency and delicate handling
The latest generation of diverters and mergers applying the dynamic motion transfer, DMT™, technology, will on display and connected to an upstream cartoning machine from RA Jones. The DMT™ diverter is capable of seamlessly balancing and distributing products at rates over 1,000 per minute.
The handling is gentle and smooth, as it is managed without gripping or queuing of the products. A large variety of products can be handled, from boxes to soft packages, including pouches.
Improved cleanliness, less cleaning time
The new wide belt conveyor (WLX) is clean, safe, and silent with good ergonomic features for line operators. Dirt collectors such as pockets and crevices have been eliminated and the design is made safe for line operators thanks to minimal openings, and the absence of sharp points and edges. Noise levels are comfortably low, benefitting the factory environment.
The integrated chain lifting function and the clever interior design drastically simplifies the cleaning process, reduces the time to clean and provides better results.
Once installed, downtime is minimal and the power, water and detergent consumption is very low. All of this contributes to a low total cost of ownership.
“In 2015, we will launch the next step of this development enabling even higher levels of hygiene and food safety applicable for direct food contact in accordance with the EHEDG guidelines” Tommy Karlsson, FlexLink’s Innovation Manager, adds.
Reduced engineering time
The FlexLink Design Tool makes design work fast and efficient. With its embedded simulation capability, the verification of the line capacity and function is accurate and made at an early stage. Thanks to the smart design method and built in intelligence, three dimensional layouts with real life appearance are safely and quickly produced. Underlying documentation such as spare parts lists is automatically connected.
Total Cost of Ownership (TCO), Innovation and Sustainability are the keys for FlexLink´s mission to increase manufacturers’ production efficiency. “All our development activities are geared for making our customers’ production processes as efficient and sustainable, thus profitable, as can be from the design phase and throughout service life” concludes Tommy Karlsson.
.
FlexLink AB
Klas Ålander
Communications Manager
+46 31 337 2499
Klas.alander@flexlink.com
FlexLink is a leading provider of automated production flow solutions – giving improved production efficiency to industry. Headquartered in Göteborg, Sweden, FlexLink has operating units in 30 countries and is represented in more than 60. In 2013, FlexLink had 840 employees and a turnover of SEK 1,664 million.
FlexLink is part of Coesia, an innovation based Group consisting of 14 companies specialized in automated machinery and industrial process solutions. For 2013, the Coesia Group had a turnover of Euro 1,370 million (forecast) and 5,800 employees.