Heating technology provider Kanthal: It’s time to electrify the steel industry
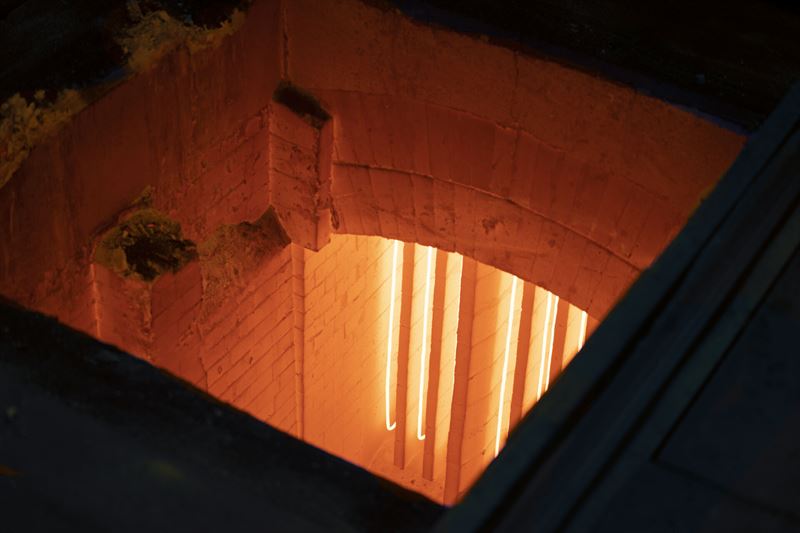
If the industry will reach its goal of fossil-free steel, it needs to stop burning fossil fuels in its heating processes. Electrification is the most promising way of achieving this, according to Anders Björklund, President of Swedish heating technology company Kanthal.
Steel remains one of the world’s most useful and in-demand commodities, yet its production processes are energy-intensive and produce vast amounts of carbon dioxide (CO2). On a global scale, the steel and iron industries account for some 7 percent of CO2 emissions. Particularly emission-intensive are heating processes, which traditionally are fueled by gas or oil. But Kanthal provides electric heating as a viable alternative.
“There are many misconceptions about electric heating. For instance, that it’s not able to reach certain temperatures. But with our technology, covering furnace temperatures up to 1500°C, you can electrify any heating process in steelmaking,” says Anders Björklund, President of Kanthal. “As we have proved, Kanthal has the technology, the thermal expertise, the resources and the global footprint to electrify all the highly energy-intensive heating processes.”
In addition to eliminating CO2 and NOx emissions and improving thermal efficiency, electric heating also provides precise temperature control. The reduction of noise and exhaust gases means a cleaner, quieter production process and work environment.
“While current heating technology is predominantly gas-fired, electric heating processes offer unique opportunities to reduce use of fossil fuels while increasing thermal efficiencies and potentially improving work environments”, says Dilip Chandrasekaran, Business Development Manager Steel, Kanthal and one of the speakers at the Sustainable Industrial Manufacturing Conference that will be held in Brussels, Belgium, June 28-29.
In the presentation, Chandrasekaran will outline benefits and advantages of electric heating within various steelmaking applications and show examples of the latest developments in this area, with specific focus on large-scale gas heating, including both modelling and experimental data.
More information about electrification of heating processes in steel production can be found on kanthal.com/electrification
For questions, please contact Yvonne Edenholm, Press and Media Relations Manager at Kanthal, yvonne.edenholm@sandvik.com, +46 72 145 23 42
About Kanthal
Kanthal® is a world-leading brand for products and services in the fields of sustainable industrial heating technology and resistance materials. The company is part of the Sandvik Group and has a strong tradition in innovation and extensive investments in R&D.
The company revolutionized the heating industry in 1931 by introducing the iron-chromium-aluminum (FeCrAl) alloy. Since then, Kanthal has launched game-changing materials and products, such as the high-power molybdenum disilicide (MoSi2) Kanthal® Super heating elements and the corrosion-resistant materials Kanthal® APM and APMT. In 2019, Kanthal launched their additive manufacturing services with Kanthal® AM100, the world’s first alloy for heating application that is specially developed for 3D-printing.
About Sandvik
Sandvik is a global high-tech engineering group offering solutions that enhance productivity, profitability and sustainability for the manufacturing, mining and infrastructure industries. We are at the forefront of digitalization and focus on optimizing our customers’ processes. Our world-leading offering includes equipment, tools, services and digital solutions for machining, mining, rock excavation, rock processing and advanced materials. In 2021 the Group had approximately 44,000 employees and revenues of about 99 billion SEK in about 150 countries.