LITRE METER SHIPS CHEMICAL INJECTION FLOWMETERS FOR GULF OF MEXICO PROJECT
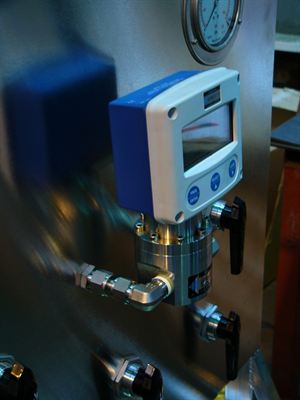
UK flowmeter specialist Litre Meter (www.litremeter.com) has shipped 40 flowmeters via its Dutch distributor ABT Bv for use in a chemical injection project in the Gulf of Mexico. The Buckingham-based company shipped two different types of positive displacement flow meters for a combination of low flow chemical injection and high flow methanol measurement applications.
The range of meters supplied demonstrates Litre Meter’s expertise and versatility in chemical injection applications.
Part of the order consisted of 34 LF05 VFF meters designed to measure three different chemicals – corrosion inhibitor, paraffin inhibitor and scale inhibitor. A further six HF40 meters were supplied to measure the flow of methanol.
Three different calibrations and ranges of viscosity were required for the LF05 meters, one for each of the chemicals concerned – 0.1 to 12l/h, 0.1 to 16l/h and 0.7 to 0.9l/h with viscosities ranging between 6.12 and 64.8 centistokes. Each meter is pressure rated to 1,035 bar and fitted with 3/8-inch autoclave engineers medium (AEM) pressure fittings.
The meters were constructed of 316 stainless steel with titanium rotors. The low flow capability of the meters has been improved by coating the pressure balance chambers and titanium rotors with physical vapour deposition (PVD) designed to lower the friction properties of the meters. The additional hardness provided by the PVD coating also improves wear resistance.
All the LF05 meters were supplied with direct head-mounted stainless steel display casings providing local display of flow rate and total with HART or Fieldbus protocols on a three-wire system mounted in an ATEX Exd stainless steel housing.
The HF40 meters were pressure rated to 1,035 bar and constructed from F55 Duplex with one-inch AEM pressure fittings. As standard these meters have a flow range of 0.1 to 2,400 l/h, a viscosity range of 0.8 to 1,000,000 centistokes and a repeatability of +/- 0.25 per cent.
Under conditions of changing pressure and temperature paraffin can build up as a waxy deposit on equipment – mostly in tubing close to the surface – and can, in severe cases, halt production. Scales such as calcium carbonate and iron oxides can also build up. Mineral salt deposits which accumulate in wellbore components due to the effects of pressure and temperature on the saturation of produced water can also cause severe blockages.
Corrosion and the loss of metal can occur anywhere in the production system from the bottom hole to surface lines and equipment. Chemicals are injected into the system to prevent these problems – and the Litre Meter LF05 flowmeters are used to precisely measure the amount of chemical being added.
Methanol is used as a hydrate inhibitor. Gas hydrates can solidify as ice-like crystals which may block the pipeline and valves, impeding the transfer of the oil and gas. This can result in a shutdown and the risk of explosion or unintended release of hydrocarbons into the environment.
Methanol is injected at high pressure where there is a risk of hydrates (dew) forming then freezing at low temperature. The process, known as bullheading, forcibly pumps methanol into the bore hole to act as an ‘antifreeze’ to lower the freezing point of gas hydrate. This protects the wells’ sub-surface valves from hydrates forming under high pressure and low temperatures during long shutdowns. The Litre Meter HF40 positive displacement flowmeters measure the flow of methanol to ensure the correct amount is injected to prevent hydrate formation.
Litre Meter CEO Charles Wemyss said: “Subsea repairs and the associated loss of production are high cost, so protecting deepwater well bores from hydrate formation, plugging and organic fouling is a major flow assurance concern in offshore operations.
“Hydrate, scale and corrosion prevention strategies provide protection during normal operation, start-up and shutdown.
“Litre Meter’s VFF flowmeter is ideally suited for use in the oil and gas industry and in particular for low flow / high pressure applications.
“Years of experience in chemical injection applications onshore and offshore have confirmed the instrument’s capability to reliably measure fluids under extreme conditions of both temperature and pressure.”