Electric railway engines, artificial intelligence, machine vision and an extensive network of wood terminals are used for wood logistics at Metsä Group’s Kemi bioproduct mill
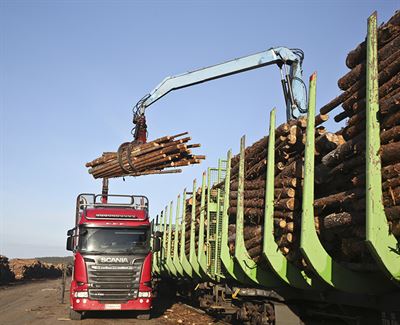
Metsä Group press release 29 November 2022
An entirely new operating method has been adopted for the wood logistics of Metsä Group’s Kemi bioproduct mill. It combines electrified rail transports, the weighing and reception of wood at wood terminals, artificial intelligence, and machine vision.
“The Kemi bioproduct mill receives two thirds of the wood it uses by train. Smooth rail logistics are essential to ensure that the bioproduct mill receives the volume of wood it needs,” says Hannu Alarautalahti, SVP, Production, Metsä Forest.
Metsä Group’s Kemi bioproduct mill will start up in the third quarter of 2023. The new mill will use 4.5 million cubic metres more wood than the current mill. The wood procurement area will also expand. According to plans, one million cubic metres of the additional wood used will be imported from Sweden.
Although the transport distances for raw wood to the Kemi mill will be longer, efficient rail transports will ensure emissions are reduced by 20 per cent per cubic metre of wood.
Several million euros invested in weighing instruments
The trains running to the mill are loaded at eleven rail terminals operated by the Finnish Transport Infrastructure Agency. New wood terminals will be set up and old ones refurbished to handle the Kemi bioproduct mill’s wood supply. The terminals in northern Finland will be completed by the end of this year and the rest by the summer of 2023.
In a new move, Metsä Group has invested in seven weighbridges for weighing timber lorries and receiving wood on arrival at the terminal instead of at the mill, as is currently the case. At the other rail terminals, the material machines that handle unloading are also used for weighing the wood.
“We have invested several million euros in the weighbridges. By measuring wood at the terminals, we can increase the terminals’ capacity and add flexibility to train transports at the mill. Moreover, timber lorry drivers can unload their vehicles at the wood terminals at their own pace instead of having to coordinate deliveries with the loading schedules of trains,” says Alarautalahti.
An indication of the importance of smooth logistics is that the Finnish railway company VR will provide carriages and engines for wood supply that will be used exclusively for the Kemi mill’s wood transports.
“We’ve planned the railway logistics and infrastructure construction with the Finnish Transport Infrastructure Agency and VR Transpoint. This transport concept was created jointly to ensure the mill’s wood supply. We piloted the operating model in the autumn and found it worked well,” says Alarautalahti.
Fully electrified unloading at the mill
“Wood delivery trains arrive at the bioproduct mill along Metsä Group’s new private track. The trains are weighed on arrival and departure with a rail weighbridge. We use dynamic weighing, which means the train does not need to stop for weighing but continues at an easy hourly pace of 8–10 kilometres along the track,” says Pasi Pulkkinen, VP, Logistics of the bioproduct mill project at Metsä Group.
“The private track enables wood deliveries by electric engines to the mill. Wood unloading at the bioproduct mill is fully electrified. These are some of the investments that will help Metsä Group achieve fossil free mills by 2030,” says Pulkkinen.
Automated unloading based on artificial intelligence and machine vision
Timber lorries are weighed on arrival and departure, as is done at all mills. What is new is that vehicles and carriages are scanned during unloading. Scanning ensures that the wood can be automatically unloaded from both trains and timber lorries. We use entirely new technology, featuring artificial intelligence and machine vision,” says Pulkkinen.
At the bioproduct mill, two autonomous woodyard cranes unload the rail carriages and timber lorries.
After the loads have been scanned, artificial intelligence linked to the crane independently plans and carries out the unloading of wood for both vehicles and carriages. Seated in the debarking department’s control room, the crane operator supervises the unloading with the aid of screens and intervenes in the unloading process if necessary.
For further information, please contact:
Hannu Alarautalahti, SVP, Production, Metsä Forest, tel. +358 50 598 7145
Pasi Pulkkinen, VP, Logistics, Metsä Group, tel. +358 40 581 0630
Krista Kimmo, Communications Manager, Metsä Forest, tel. +358 50 526 4911
Tiina Tassi, Communications Director, Metsä Fibre, tel. +358 40 833 4811
Metsä Group Wood Supply and Forest Services
www.metsagroup.com/metsaforest
Metsä Group’s Wood Supply and Forest Services provides and develops the services offered to the members of Metsä Group's parent company, Metsäliitto. The cooperative consists of nearly 100,000 Finnish forest owners who together own about half of Finland’s private forests. We provide all the forest services required to engage in sustainable forest management and raise the value of forest assets.
We procure all the wood used by Metsä Group from sustainably managed forests in the Baltic Sea region, most of it from our owner-members in Finland. We also supply significant volumes of energy wood, bark and sawdust for further processing.
In 2021, our sales totalled EUR 2.0 billion, and we have around 850 employees.