Premier Waste UK disposes of unwanted alarms thanks to Notifier
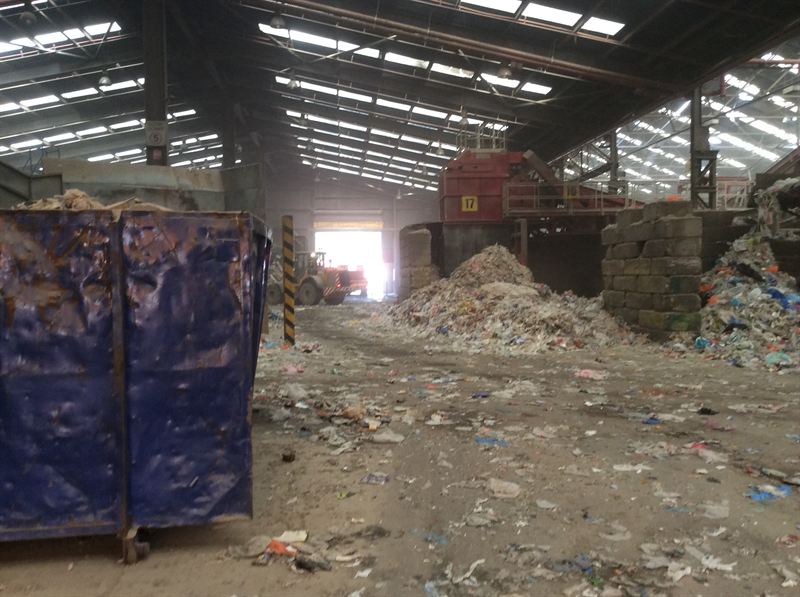
With high levels of dirt and dust, waste recycling plants are challenging environments for life safety systems to operate in. Disruption from unwanted alarms can result in unnecessary costs, such as waste redirection, moving stored materials to safety and process downtime. This makes the use of ultra-reliable and accurate fire detection essential.
Premier Waste UK is the nation’s leading provider of waste recycling services and, not surprisingly, its 200,000ft² facility in Birmingham combines dust and moisture in very high levels. A misting system is in constant use to damp down dust and deal with odour issues, and the processing of construction and commercial waste, including packaging, creates a considerable fire hazard.
To monitor the facility Premier Waste UK has over 15 fire marshals to carry out checks every 60 minutes, as well an on-site fire engine with a water tank holding in excess of 620,000 litres of water, along with five fire hydrants. Having previously used heat detectors to monitor the site, Premier Waste UK was experiencing a high instance of disruptive unwanted alarms – as frequently as every other day – along with a potential timing delay from waiting for the amount of heat to spike quickly enough to trigger the system.
Premier Waste UK’s Operations Director, Wayne Clark, explains, ‘It was clear that the use of heat detectors didn’t provide the earliest warning that would allow us to minimise the problems caused by fire events. Therefore, we worked with Advanced Fire Solutions to come up with an alternative and it was clear that aspirating smoke detection would be the only technology that could cope with the extreme environments we face.’
Environmental conditions at the plant can fluctuate considerably from area to area and whole plant monitoring was required. After assessing what the aspirating smoke detection market could offer, Premier Waste UK decided that Honeywell’s FAAST system, controlled by Notifier’s innovative Pearl control panel, would offer the most effective solution.
The FAAST system consists of an enclosure, housing the electronics that are powered from a supply, and a fan inside it that draws air in via pipes that are connected to the unit. The air that is drawn in then goes through a unique patented filtration process. It then passes across a dual source blue LED and infrared laser projected into the air itself and, if enough smoke particles are detected, an alarm condition is activated. FAAST’s pipework contains sampling holes at predetermined locations, through which the air is drawn and with a level of sensitivity 300 times greater than a traditional smoke detector, issues can be quickly dealt with before having to evacuate the facility.
Asked to explain why FAAST was selected over comparable devices, Clark replies, ‘The combination of accuracy, ultra-sensitive detection and proven unwanted alarm immunity in high dust/moisture environments made FAAST the most attractive option for us from a safety perspective. Added to this was ease of installation and the ability for in-house personnel to carry out maintenance. FAAST is also great because it auto-learns the environment and can be used across the whole plant – it remains stable even in fluctuating conditions.’
The FAAST system is complemented by the Pearl control panel, which offers best in class performance, scalability and functionality. The networkable fire alarm control panel is available in one or two loop models and has been specifically created to be immune from the threat of unwanted alarms, even in challenging environments where there is a high likelihood of them occurring.
‘Pearl uses a digital protocol to increase efficiency, reduce power consumption and enable a set of features to improve the system diagnostics, control and usability,’ comments Derek Portsmouth National Sales Leader UK & Ireland at Notifier. ‘It provides a highly resilient system with powerful networking capability thanks to Notifier's superfast ID²net. This can communicate a fire signal across a network of up to 16 panels and 20,000 devices in less than one second.’
Premier Waste UK’s Wayne Clark is delighted with the impact of the FAAST and Pearl solution, and concludes, ‘These products have exceeded all expectations and I can’t remember the last time we had an unwanted alarm. Aside from its performance and ease of use, the entire system is easy to maintain and has also helped us reduce our operational costs, whilst enhancing safety. When a fire event occurs, we can now respond much quicker, and this reduces business interruptions as well as risks. Honeywell has provided us with a solution designed to exceed insurance and legislative requirements and we are really delighted with the result.’
For further information please call 01444 230300 or visit www.notifierfiresystems.co.uk