Stora Enso Imatra – Web Inspection / Defect Detection System Upgraded to Improve the Quality of Board Machine #4
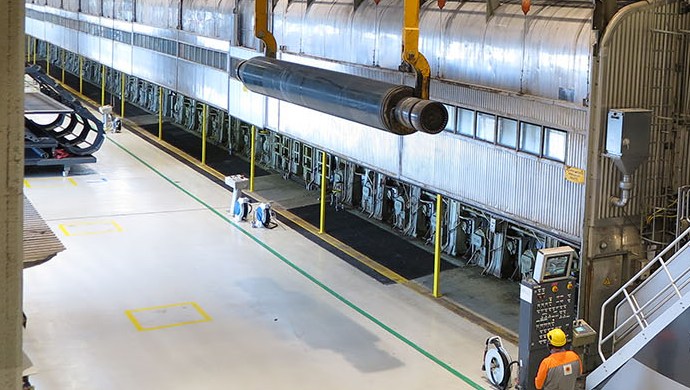
Stora Enso Imatra Mills introduced the Procemex web inspection and web monitoring system. The system helps Stora Enso to better investigate the root causes of web breaks, reduce the number of breaks and increase production efficiency.
Stora Enso Imatra Mills is the largest manufacturer of liquid packaging board in the world. Consumer packaging board used in contact with food and liquids must meet strict quality requirements set for food safety. What is more, no flavours can dissolve from the board into food products, and the products must be first-rate in terms of visual cleanliness.
For several years, systems supplied by Procemex have been used in Stora Enso's board machine 4 (BM4) to indicate any defects in board quality and to reduce web breaks. In March 2016, Stora Enso Imatra Mills made a system modernisation investment to improve the quality of food packaging board and increase the efficiency of the board machine.
Why did you decide to upgrade your system?
“We compared three different suppliers and ended up with Procemex, first of all, because we have had positive experiences with the previous system and, secondly, because we were able to upgrade the previous system – without needing to acquire a completely new one. We also investigated what benefits we can gain from the upgrade. In the end, the decision was an easy one; after all, we obtained a wholly new system by simply upgrading the old one,” says Mr. Riku Suurnäkki, Production Manager of BM4.
“Both web break and web inspection/defect detection systems are critical elements in order to be able to operate these machines: web inspection in terms of the final cleanliness and the web break system in terms of production efficiency. If we encounter any problems with efficiency, the web break system allows us to identify the root cause of breaks, enabling us to resolve, or even eliminate, the problems.”
Stora Enso Imatra Mills defined new locations for cameras, together with machine operators, and, now, cameras indicate the locations where pulp starts to pile up. “Of course, it is essential to listen to users,” Suurnäkki says.
“The new system became a necessity after we identified that we need to improve the classification of defects and the usability of the system. The previous system was unable to reliably classify a certain common defect, and there were situations in which defects in board ended up in our plastic coating,” says Suurnäkki.
What benefits did the upgrade produce?
The new upgraded Procemex cameras have a significantly higher resolution, defects are now classified more closely, the detection of defects is now more visual and the system is easier to configure for each user.
“We can better detect any dirt and impurities,” says Vesa Koskinen, system specialist at Efora, who is responsible for the maintenance of the BM4 system.
Project management at the core
“On our part, the project did not get off to a textbook start, and we were forced to speed up the process. Procemex did an excellent job, even though the order-delivery schedule was very tight. The installation period was also tightly regulated and brief, but Procemex was able to ensure the resources required,” says production manager Riku Suurnäkki. “Commissioning, adjustments and links to mill systems – everything was done on time.”
User experiences
“The experience we have had so far indicate that the detection of defects is now much more visual than in the previous system, and the classification of defects has improved. Operators have already given us direct positive feedback, saying that the image quality is on a completely different level and, therefore, there are fewer web breaks,” Riku Suurnäkki says.
Usability and maintainability
“When acquiring new systems, usability and maintainability are among the most important criteria in order to keep our expensive machines and systems up and running. Cameras need to remain clean and the image quality must be high. The supplier must be quick and easy to reach,” Suurnäkki says, listing the criteria set for the new system.
“The new system improved overall reliability. We acquired new PCs and upgraded our cameras. Shifting to the new system was a simple process,” Vesa Koskinen says. “These Procemex Pinhole cameras are excellent, and they practically require no cleaning. The Pinhole cameras are in challenging locations, where pulp keeps flying every which way, but they are easy to keep clean. The new Procemex cameras offer an HD quality, the images they produce are on a whole different level, and lighting has been improved by using new Procemex LEDs. These new lights are much easier to control than the old ones.”
“It is easy to call Procemex whenever we need help, and it quickly responds to our questions,” Vesa Koskinen says.
Remote maintenance reporting
Stora Enso is using the Procemex remote reporting system, which offers preventive information, for example, about system performance, camera image quality, the operation of IT hardware and backups – it is a maintenance tool. The system produces monthly reports, creating comprehensive information about maintenance and raising a need for various tasks. “Procemex has very short delivery times for spare parts; of course, with the help of the preventive remote reporting system,” Koskinen says.
Continuous development
“We have new development projects in progress all the time, but we cannot say anything more about them at this stage. As requirements are becoming tighter and tighter, there is always something to improve. Procemex is an excellent partner in these projects.”
For more information:
Stora Enso, Imatra, Riku Suurnäkki, Production Manager of BM4, tel. +358 40 5845544
Efora Oy, Vesa Koskinen, System Specialist, BM4 defect detection system
Procemex, Kristiina Pispala, Marketing Manager, tel. + 358 40 191 8882
Procemex, Ari-Pekka Räisänen, Director, Product Development and Customer Service, tel. + 358 50 313 7243
Stora Enso Imatra:
Stora Enso Imatra Mills is the largest manufacturer of liquid packaging board in the world. Imatra Mills consists of two mill units: Kaukopää and Tainionkoski. Together, these units employ approximately 1,000 people. The annual capacity of Imatra Mills is more than one million tonnes of board and paper. More than 90% of production is exported. The company's main market areas are located in Europe, while Southeast Asia forms another significant region.
Imatra Mills produces board and paper. Stora Enso manufactures liquid packaging board for milk and juice cartons, among others. Food packaging board is used to manufacture cups and different food packages. Packaging board is used in food, candy and cigarette packages. Package covers, cards and luxury packages are made from graphic board. Imatra Mills also manufactures packaging paper.
Tags: