Allison Automatics make sugar cane harvesting sweeter
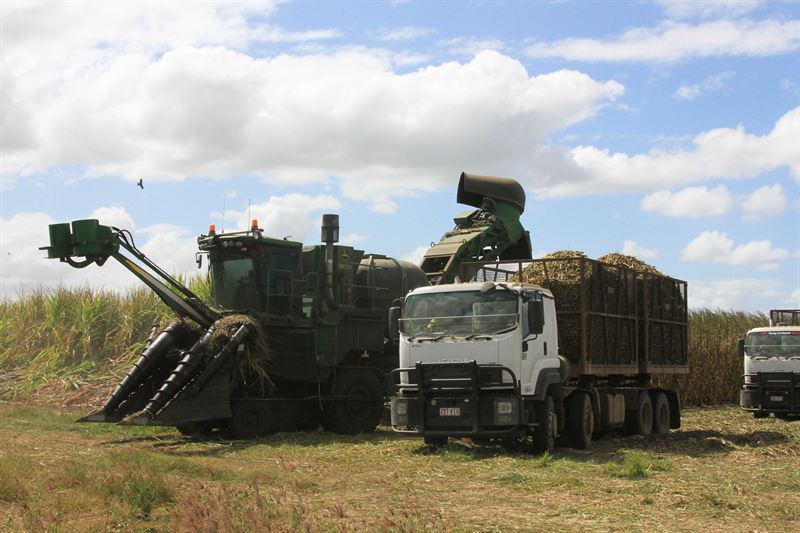
Replacing 1,300 manual gear changes over 11 hour shifts, a major North Queensland sugar producer has purchased three new twin-steer Isuzu FYH trucks equipped with Allison fully automatic transmissions to simplify driver recruitment, reduce driveline damage and improve efficiency
AYR, Australia – Green Acre Harvesting recently purchased three new twin-steer Isuzu FYH trucks equipped with Allison 4430 six-speed fully automatic transmissions to simplify driver recruitment and improve transportation efficiency for its cane harvest.
Until recently, success of the heavy-duty Isuzu rigids with the Allison 4000 Series™ automatic transmission had primarily been in construction, concrete mixer and road tipper applications. However, the use of the Isuzu FYH automatic in transporting harvested sugar cane underlines the versatility of the overall package and its ability to be adapted for a number of vocations.
As a long time sugar producer based near Ayr, owner Richard Galea has seen significant advances in technology. From heavily labour-intensive manual cane cutting by teams of men wielding long knives to today’s fully-automated harvesting with modern automatic diesel trucks to transport the cane, efficiencies have greatly improved.
Galea purchased the new automatic Isuzus to work on the cane harvest, which runs each year from June until November and will see more than 146,000 tons of sugar harvested from close to 4,000 farmland acres annually.
“One of our biggest challenges is recruiting drivers,” said Galea. “The automatics allow us to hire drivers that might not be as experienced or skilled. We can train them and will not have to worry about damaged clutches and drivelines, which was a problem with our old manual trucks.”
The Allison-equipped Isuzus replaced three ageing Volvo F7 manual trucks and in the four months since joining Green Acres, each of the Isuzus has travelled more than 10,000 miles and logged 1,400 hours of operation.
“The trucks are fool-proof,” said Galea. “In the past, we have had problems with clutches and drivelines coping with maintaining a slow speed while tracking alongside the harvester in the paddock, but that is not a problem with Allison Automatics.”
During the harvest the trucks work seven days a week, from 3 a.m. through to 2 p.m., in a relentless sweep of the paddocks, driving alongside the automated harvester, which loads directly into the cane hoppers on the back of each truck. The cane hoppers are fitted with rail wheels and are winched onto the back of the trucks and secured at the rail siding. The truck then travels back to the paddock with the empty hoppers and catches up to the harvester. With three trucks the harvester can continuously move through the cane, slowing briefly as one truck is filled and another moves under its loading spout to continue cutting and removing the cane.
Once the hoppers on each truck are filled, it drives back to the rail siding where the full hopper carriages are backed up to the railway line and released onto the line to be hauled away by a cane train later in the day. The driver then winches two more empty carriages onto the back of the truck and heads back to the harvesting area for yet another load.
It is an unrelenting schedule, but necessary in order to meet the local sugar mill’s appetite for raw sugar cane. According to driver Ivan Rehvein, the new Allison-equipped Isuzus have made his job much easier.
“The ground has been covered by 6-foot-high cane for many months, so it is often a bit soft and boggy. The new automatics make maneuverability much easier,” said Rehvein. “They are a godsend when you’re backing up and turning. It is so much easier than operating a manual and that makes the work a lot less stressful.”
Concentrating on keeping pace with the harvester, while not having to worry about selecting the correct gear when tracking through the often soft-soiled cane paddocks, has made the driver’s work less taxing.
“On a typical day we made close to 1,300 gear changes in the old manual Volvo trucks, which meant you were constantly working the gearstick, but now with the new automatic Isuzus we don’t have to worry about that and we are a lot less fatigued at the end of an 11- or 12-hour shift,” he said.
“We can just sit the Isuzu on 1200rpm, push the button and hold the gear. We drive alongside the harvester without having to worry about slipping the clutch or being in the wrong gear, because the Allison Automatic does all that work for you,” said Rehvein
About Allison Transmission
Allison Transmission (NYSE: ALSN) is the world’s largest manufacturer of fully automatic transmissions for medium- and heavy-duty commercial vehicles and is a leader in hybrid-propulsion systems for city buses. Allison transmissions are used in a variety of applications including refuse, construction, fire, distribution, bus, motorhomes, defense and energy. Founded in 1915, the company is headquartered in Indianapolis, Indiana, USA and employs approximately 2,700 people worldwide. With a market presence in more than 80 countries, Allison has regional headquarters in the Netherlands, China and Brazil with manufacturing facilities in the U.S., Hungary and India. Allison also has approximately 1,400 independent distributor and dealer locations worldwide. For more information, visit allisontransmission.com.
Press Contacts
Claire Dumbreck Holly Zhang
Propel Technology Allison Transmission Asia Pacific
claire@propel-technology.com holly.zhang@allisontransmission.com
+44 (0) 1295 770602 +86 (10) 6468-6800, ext 8818
Unit 4, Manor Farm Offices Room 319, Block C. Guomen Building
Northend Road, Fenny Compton #1 Zuo Jia Zhuang, Chaoyang District
Warwickshire, UK Beijing 100028, China
Tags: