Eight of ten truck standstills can be avoided with preventive maintenance
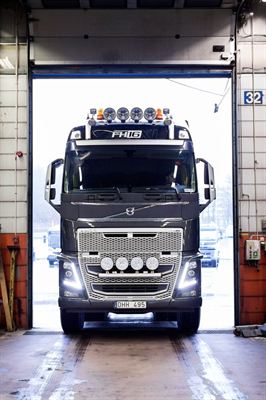
The number of unplanned truck standstills can be cut by 80 per cent. This is revealed in a study conducted by Volvo Trucks. In the long term, the aim is that unplanned standstills should entirely disappear. One key explanation for this expected trend is online connectivity in trucks, a development that creates entirely new scope for working with preventive maintenance.
An unplanned standstill is one of the most problematic issues that can affect a haulage firm. Apart from the inconvenience for the driver, it creates extra costs for repairs, lost transport revenue and, in the worst-case scenario, a damage to customer reputation.
“Since the transport industry already operates with very small margins, an unplanned standstill hits haulage firms hard. We therefore have to be better at understanding why unplanned stops take place and help both customers and drivers increase their productivity and thus also their profitability,” says Hayder Wokil, Director Quality and Uptime, Volvo Trucks.
In order to increase knowhow about how to help haulage firms boost their productivity, Volvo Trucks conducted a comprehensive survey that based on real-life user data from 3500 Volvo trucks gathered over a 5-year period. With this authentic statistical basis the company then conducted advanced simulations and generated a variety of possible service situations to analyse how, why and when trucks suffer unplanned standstills. The aim was to find out how unplanned stops can be avoided.
“The study clearly showed that by being able to monitor the truck’s usage and the current status of the vehicle’s various key components, it is possible to plan maintenance better. We reckon we can reduce the number of unplanned standstills by 80 per cent if the truck is serviced in time and in response to actual needs,” explains Hayder Wokil.
Connected trucks are the way to zero unplanned standstills
One important prerequisite for reducing the number of unplanned standstills is to be able to predict maintenance needs and to tailor servicing for each individual truck. This is possible since today’s trucks can be connected online to the workshop.
“For instance, a service technician can remotely monitor exactly how the truck is being used in real time, schedule maintenance well in advance before something breaks down, or order spare parts in advance. What’s more, a scheduled service can also be postponed if the workshop technician can see that the truck’s various components are subject to less wear than expected, thus saving time for both the haulage firm and the driver,” relates Hayder Wokil.
Although Volvo Trucks has made considerable progress in this area, Hayder Wokil feels that the development of preventive service is still in its infancy.
“We see considerable potential in this area. Connected vehicles are the route to zero unplanned standstills in the future,” says Hayder Wokil.
See the film on Volvo Trucks' YouTube channel (link)
Download images at Volvo Trucks’ Image Gallery (link)
Facts
Unplanned standstills
- The truck cannot carry out a planned assignment owing to a fault with the vehicle. This is the opposite of the truck being available for a transport mission (usually expressed as ‘Uptime’).
- A Volvo Trucks study reveals that the average cost of an unplanned standstill is approximately 1000 euros for a haulage firm in Europe (this includes direct costs such as towing and repairs, administrative fees, any fines involved, and lost transport revenue, but not costs in the form of destroyed cargo or lost income owing to a ruined reputation).
Here’s how the survey was carried out:
- The survey (evaluation and simulation) has been performed by the department for Advanced Technology & Research (ATR)” at Volvo Group, working with research within among others uptime and aftermarket solutions.
- Based on real-life user data from 3500 Volvo trucks collected over a 5-year period. The vehicles each covered more than 120,000 km a year.
- Based on the user data, simulations were carried out to find out how unplanned standstills can be avoided.
- Examples of information obtained: how the truck has been used, for instance brakes, which breakdowns have occurred.
Connected trucks:
- This means it is possible to remotely communicate with the truck.
- Generates opportunities from several perspectives: for the haulage firm owners, drivers, service workshops, and society in general in the form of increased productivity for the transport sector, with better traffic flow and less environmental impact.
- Several of the services within Volvo Trucks Services, for instance in transport management, fuel management, and uptime-related services, are possible thanks to online connectivity.
- The Volvo FH16, Volvo FH, Volvo FM, FMX the Volvo VN range, VHD and VM can all be linked to Volvo Trucks connected services.
May 19, 2015
For further information, please contact:
Ida Mattsson, Volvo Trucks Media Relations. Phone: +46 31 323 63 42, e-mail: ida.mattsson@volvo.com
For broadcast-quality videos supporting this press release and more, please visit http://www.thenewsmarket.com/volvotrucks
Press images and films are available in the Volvo Trucks image and film gallery at http://images.volvotrucks.com
Volvo Trucks provides complete transport solutions for professional and demanding customers, offering a full range of medium to heavy duty trucks. Customer support is secured via a global network of 2,100 dealers and workshops in more than 140 countries. Volvo trucks are assembled in 14 countries across the globe. In 2013 more than 116,000 Volvo trucks were delivered worldwide. Volvo Trucks is part of the Volvo Group, one of the world’s leading manufacturers of trucks, buses and construction equipment, and drive systems for marine and industrial applications. The Group also provides solutions for financing and service. Volvo’s work is based on the core values quality, safety and environmental care.
Tags: