Kiilto takes on biggest challenges faced by manufacturers of multilayer flooring
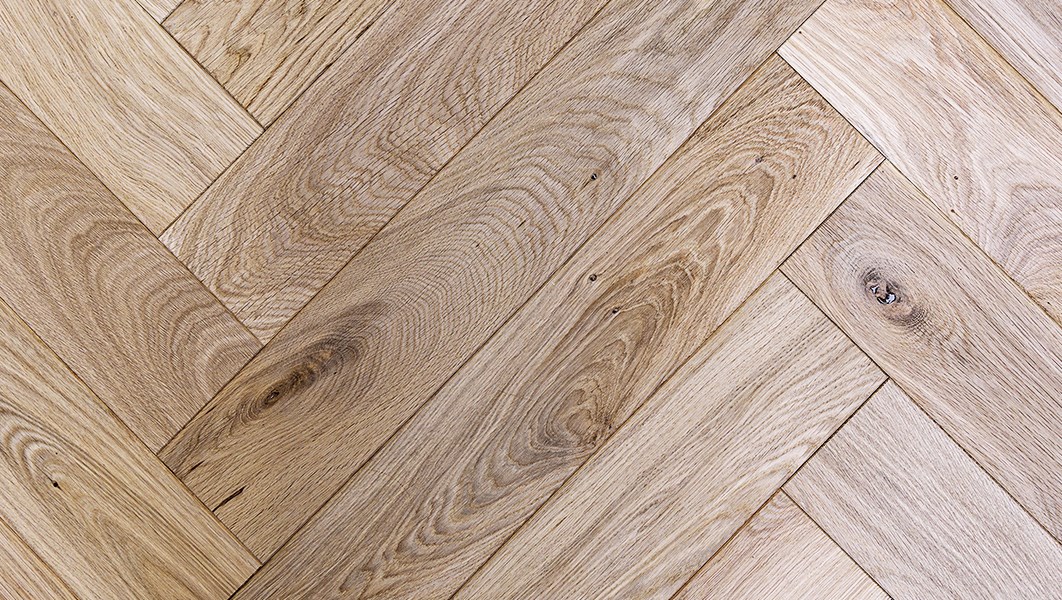
The expectations placed on manufacturers, as well as on multilayer flooring materials themselves, keep getting higher and higher. Buyers are becoming increasingly demanding in terms of aesthetics, forcing many companies to use different types of wood, including exotic wood, which poses many production challenges.
Exotic wood – a challenge for the bonding process
Exotic wood is more difficult to process and very demanding in terms of choosing an adhesive. Its anatomical structure and the presence of residual substances can result in reduced adhesion, which greatly hinders the bonding process.
Another problem is increasing the strength and endurance of multilayer flooring due to its use in different types of rooms and the effects of underfloor heating. Other important factors include the location of the flooring (will it be in contact with water or exposed to sunlight?) and conditions such as humidity and cyclical (daily or monthly) changes. Exposure to sunlight causes the surface to heat up, especially when it comes to dark-coloured floorboards. It is important to choose the right adhesive when producing multilayer flooring. This is because the current trend is to have large terrace and balcony windows, which expose floors to plenty of sunlight and, after sunset, a drastic and rapid drop in temperature. This creates a large amount of thermal stress for the adhesive to withstand. In such cases, adhesives that comply with WATT '91 (DIN EN 14257) are required.
Bonding the middle layers
An important aspect is the use of different cores to increase strength. These can be made of solid wood (usually of lower grade or quality), plywood and HDF, which is increasingly common. For the middle layer, pine, spruce or wood from the processing waste of the top layer is usually used. In the case of pine, a problem we often encounter is the presence of a large amount of resin or other wood defects (e.g., knots). This can weaken adhesion and make it difficult for the adhesive to penetrate deep into the material, which can loosen the bonding. This most often only becomes apparent when the flooring is being used.
The use of plywood and HDF cores poses many problems for manufacturers, from the machining process to bonding. Using wood-based cores in flooring very often leads to deformation, such as curling and warping, which means that the finished product cannot be used. Such materials require manufacturers to use fast-setting adhesives with a high solid content and initial grab, which provide a strong adhesive bond and prevent deformation. The surface of an HDF core can pose yet another problem, namely that it reduces an adhesive's ability to bond to it. A straightforward solution would be to use adhesives with a broad spectrum of bonding properties, which adhere very well to many difficult materials (including HDF cores).
It would be advantageous for multilayer flooring manufacturers to know exactly how their products would be used and where they would be located. Typically, however, manufacturers lack such information, so they need to cater for all kinds of possible uses and scenarios, which can sometimes be far removed from their products' original intended purpose. This makes it a necessity for them to use the best surface finishing, processing and bonding technologies.
Importance of bonding during the manufacturing process
The bonding process significantly affects the quality of the finished product, even though it represents a small part of the product cost. That is why it is crucial to use top-quality and appropriately chosen adhesives to bond materials together.
Kiilto offers a wide range of extremely versatile adhesives for the manufacture of multilayer flooring materials. Using these adhesives ensures that bonding of the highest quality is achieved. Safety in production and use is also an increasingly important aspect. That is why many Kiilto adhesives have the M1 certification, which ensures that emissions of all volatile organic compounds (VOCs) are at very low levels not exceeding 0,2 mg/m2h. M1-certified adhesives makes the finished multilayer flooring safe to use.
Productivity sprint with Kiilto’s new D3 PVAc adhesive
One of Kiilto’s latest offerings for wood flooring manufacturers is the Kestokol D 320 HF adhesive, whose formaldehyde content falls below 20 ppm, as specified in ISO 15373. It serves as an alternative to the ever-popular urea-formaldehyde products without compromising bonding performance and quality. It is the perfect adhesive for flooring production in hot press lines and increasingly used high frequency (HF) presses. It facilitates a very high level of productivity with an up to 40-second press time and extended open time, which allow for continuous production that's always “online”. This product performs with a high thermal resistance WATT '91.
Contact us for more information!
Tags: