Simplify your business system
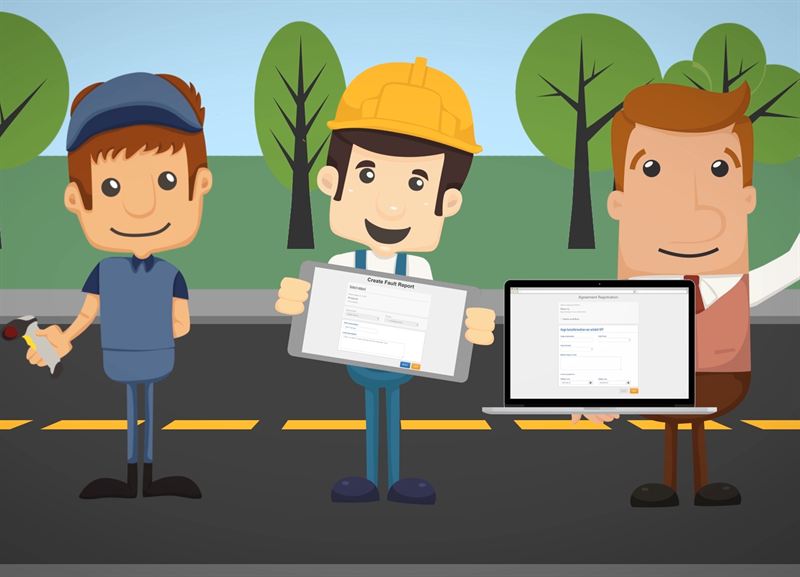
A tool should make work easier for the person doing it. Companies need tools in order for their employees to be able to carry out their tasks, and to plan so that everything is done in the right order. Together, these tasks are known as processes – or business processes – and, of course, all companies need control over their business dealings. Processes are found everywhere within a company, including stock management, production, marketing, sales, maintenance, etc. Good control also brings opportunities to evaluate and improve these processes. If processes and evaluation are dealt with effectively, this control leads to more satisfied customers and doing more profitable business. So far so good! But the problem is that things are rarely this simple.
Almost all companies have some kind of business system. Well-known business systems include SAP, Oracle, IFS Applications and Agresso. One thing that all business systems have in common is their ability to deal with transactions that make business processes possible. A transaction in a business system means that a certain value is changed to another value. For a transport company, this could involve moving a crate from location A to location B. For a service company, it could involve reporting a job as completed.
Business systems are based on transaction management, not necessarily how the business is carried out. So how can the crate in the first example be moved from A to B in the best possible way? How should the job in this particular situation be reported? It is in these questions that business systems reveal their weaknesses. The actual transactions are dealt with in virtually the same way, regardless of the company. However, there are big differences in the way different companies work, and in the way their employees carry out processes. The bigger the company, the more complex the systems. And a company can have various different systems – warehousing systems, HR systems, sales systems, and so on – making the situation even more complex.
For many companies, the reality is that they use complicated business systems because of the complexity of what they do. This often results in their systems being difficult or slow for users to work with. Tasks such as measurements, follow-ups or evaluations can be unnecessarily time-consuming or convoluted. So a business system that looks fantastic on paper and aims to streamline an operation can actually result in a long and sluggish work process. The tool – or business system – that was supposed to make tasks easier actually has the opposite effect.
So are all investments made by companies in various business systems unnecessary? Not at all. A business system can be easy to work with. But it’s important to take more than just the transaction perspective into account when starting to use a business system.
In order to succeed in making a business system an effective tool, both the business and the user’s way of carrying out tasks must be taken as starting points. Only then can a tool be created that allows the user to carry out processes with the anticipated results and effectiveness.
Based on this overall perspective, NovaCura has developed a platform that gives companies the freedom to design their own tools according to their unique way of working. The platform, NovaCura Flow, works as a layer between the company’s business system and its users. Flow can be connected to absolutely any business system. It’s no exaggeration to say that NovaCura Flow helps companies to save huge sums of money by making more efficient use of time. Every day.
How NovaCura Flow® works
NovaCura Flow differs from business systems, being a program that is added as a shell on top of the system. In other words, Flow is not a new business system.
The way in which Flow can quickly be connected to the business system in view of the existing work process is both simple and innovative. A work process usually also involves certain limitations that create different conditions, such as the work having to be done using a computer with a network connection. Or there may be limitations on the surroundings or the order in which the work has to be carried out.
With NovaCura Flow, the user is not dependent on adapting the work or the system to suit a particular type of computer or apparatus. Companies are completely free to choose how they want to work and at which unit. There is virtually unlimited flexibility, and the users get an environment which helps them to work instead of hindering them.
It only actually takes a couple of days for NovaCura to transform a business system into a simple and effective tool. The methodology on which NovaCura Flow is based is just as simple as it is intuitive, and always begins with a workshop together with the customer company.
A process or a workflow is selected where the company wants to improve efficiency.
The workflow is analyzed during the workshop. Improvement measures are identified, and a new, better workflow is drawn using Flow Designer, NovaCura’s own drawing tool.
Any duplicated work or logical errors in existing processes can be eliminated during the process mapping stage.
In NovaCura Flow Designer, the new workflow is configured with the necessary user interface and system integration points.
The workflow is then published in a new application which is created directly from the drawn flow, and the customer can begin working more effectively straight away.
One significant advantage with this approach is that the customer has to think through his processes, and can work together with users and NovaCura to create new behaviours that lead to real process improvements. The customer has an application to evaluate immediately after the workshop, and NovaCura Flow can be fully implemented within just a few weeks.
The effect is immediate. Once a company’s work process are working without obstacles and using an intuitive interface, its work flows efficiently and with clear results in the form of improved efficiency, time savings and customer and staff satisfaction.
NovaCura Flow turns complicated business systems into straightforward workflows.
How some of our customers work today
Dalkia
NovaCura makes life easier for Dalkia’s customers and employees.
The company now has a faster work process with less duplicated effort, a minimized risk of errors and employees who are more mobile than ever before. These are just a few of the advantages of NovaCura’s solutions for Dalkia Nordic.
Dalkia Nordic is a world-leading optimized resource management specialist. The company provides solutions within energy, water and waste, and helps towns and industries to make the most of their resources. Its customers are usually the owners of complex properties, industries or energy plants, and often need the unique expertise of Dalkia’s engineers. Customer benefit and customer value are guiding principles in Dalkia’s values, and it is crucial that the company’s engineers are always on-site as soon as possible.
With the help of NovaCura Flow, Dalkia has therefore created a system enabling all its mobile engineers to carry out all their work tasks using a tablet. This has streamlined the company’s work enormously, as its engineers no longer need access to computers. All work orders were previously obtained from shared computers at the office, but the engineers can now get their orders while on the road. Today, the company’s engineers are entirely location independent.
However, NovaCura’s efforts to simplify everyday life for Dalkia’s employees go even further. Their work will become even more effective thanks to the customer portal for fault reporting that NovaCura has developed for Dalkia.
Previously, Dalkia’s customers reported faults to Dalkia, who in turn forwarded the information to the relevant part of its service organization. This involved unnecessary duplicated work for staff, and meant customers had to wait an unnecessarily long time for faults to be rectified. NovaCura’s solution was to link together all the existing parts of the system, creating a brand new customer portal. Customers can log in to the new portal and generate their own fault reports, which are sent immediately to the appropriate person at Dalkia.
Mobile engineers then receive work orders directly on their tablets, including details of the customer, the type of fault, where the fault has arisen and contact details. Tasks are automatically allocated according to the parameters ‘Available’, ‘Right expertise’ and ‘Nearby’.
“Our customer portal allows customers to monitor our engineers’ actions in real time, as the engineer uses the tablet to provide updates,” explains Dalkia’s Site Manager Jan Walldorf. “We’re on site promptly, the customer gets a quick response, and in most cases we can process a fault report through to invoicing on the same day.”
For Dalkia, the customer portal has resulted in faster processing, better quality and improved customer satisfaction. The customer can use the portal to follow the entire process, from fault report through to rectification, and sources of error are minimized as the information only needs to be input once. In brief, NovaCura’s customer portal has made everyday life easier for both customers and staff.
“Our customers are no longer dependent on our opening hours, and can place an order without having to wait in a telephone queue to contact customer service,” adds Kristina Nerg, Chief Controller at Dalkia Nordic. “Most customers also use the portal for other purposes, such as checking the status of their work orders and document links. The fact that customers register work orders themselves has eliminated a stage in our work process.”
New workflows for Minco
Minco designs and manufactures advanced components for the medical, aerospace and defense industry globally.
When customers, offices and manufacturing are located throughout the world, it is crucial that deliveries are correct. But despite meticulous processes, Minco’s customer requirements were not being met, which sometimes resulted in complaints and tedious return processes. The same applied internally: inventory on shelves and in Minco’s ERP system were not always consistent. It all came down to the human factor, as all transport tasks were handled manually and a small mistake could mean huge consequences.
As a result, Minco started to look for a barcode solution so that employees could easily scan products before shipping to verify product is correct and going to the correct customer, as well as upon delivery.
“We wanted a solution for processes both in and outside our ERP system. Sure, it was possible to customize our current processes, but it would be expensive”, said Business Analyst Matt Hanson.
As soon as he received a demonstration of NovaCura Flow, he realized that this was the right solution. And after a 30-day trial, he was convinced.
“In the first week, we implemented four workflows and got a custom-made product that was both affordable and easy to customize.”
Today, 28 employees are using NovaCura Flow, primarily in stock and inventory, and they have a total of 18 hand-held devices and multiple desktop scanners at the computers. The time saving is important, but that’s just the beginning, says Matt Hanson.
“The stockroom group saves time and steps, which is good for flexible processes. But above all, we see that the discrepancies and the returns are going down – we simply have more satisfied customers now.”
Another benefit for Minco has been all of the development opportunities. NovaCura’s U.S. branch, Enterprise Consulting, was asked if they could train one of the developers at Minco so that they could construct smart workflows internally. It was a success, says Michael Tapper at Enterprise Consulting.
“We arranged a workshop that combined training for Minco’s developer Jeff with building the actual workflows for production use. Following the two day workshop Jeff was trained and able to build his own workflows, plus the workshop resulted in two workflows being built and deployed into production.”
And since then, the developing has continued. Minco now has 13 customized flows, ranging from cycle counting flows to individual time reporting on shop orders, something that had been requested but had not been possible in the current version of IFS Minco is using. In addition, they have constructed worksheets that can be managed with Android tablets for the Quality Assurance department – they can now compile and transmit digitally and directly to management during an audit. Minco has added 60 additional licenses for a total of 78 to roll out the additional functionality to more users, and has plans for 100 additional licenses for the time reporting function.
Matt Hanson has also received inquiries from the finance and purchasing department, because they want to automate and simplify their processes, such as sending invoices to customers.
“I see a lot of future applications of NovaCura Flow at Minco”.
Specma
NovaCura’s bar code scanners allow Specma to work 30 percent more efficiently. There is plenty of scope for things to go wrong in an enormous warehouse with many similar looking items. But thanks to NovaCura’s bar code scanners, Specma Hydraulic can now be confident that their customers will receive the right goods. What’s more, they’ll also receive them faster.
Specma Hydraulic is the Nordic region’s leading supplier of application-based hydraulic systems and hydraulic, pneumatic and conduction components. The company, which constantly strives to improve, discovered that it could benefit from an improved warehousing process and decided to engage NovaCura. The solution involved implementing NovaCura Mobile Solutions’ bar code system, leading to increased warehouse productivity and improved delivery reliability for customers.
“We have many different products,” explains Aksel Jarlbäck, IT Manager at Specma Hydraulic, “and many of these are similar in appearance. Scanning bar codes allows us to be sure that the item number corresponds with the actual item. The system tells us if an error has been made. The solution has enabled our warehouse workers to improve their efficiency by around 30 percent, and there has been a dramatic drop in errors.”
The new warehousing process features high levels of orderliness and quality, since all data is only recorded once, and the system takes care of many jobs that were previously carried out manually. The system also reports directly into the business system, allowing Specma Hydraulic to carry out inventorying at any time without having to call in additional staff.
För ytterligare information
Johan Melander, Managing Director Novacura, 073-850 11 11, johan.melander@novacura.se
Magnus Sjöbäck, Press officer Novacura, 0704-445 15 99, magnus@sjoback.se
NovaCura is a humane-centric IT-company using services and software to streamline and simplifie their customers’ business-critical processes and ERP platforms. NovaCura is privately held and has offices in Sweden and Poland. Their software solutions are sold through partner companies in Europe and the U.S. NovaCura has 40 experienced employees and is headquartered in Gothenburg, Sweden. www.novacura.com
Tags: