ABB presenterar YuMi®, världens första samarbetande tvåarmade robot
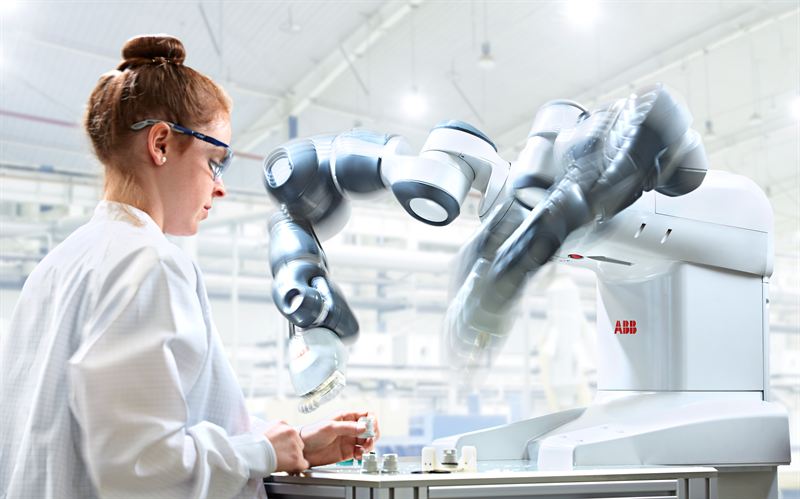
YuMi, ännu en innovation enligt ABB:s strategi Next Level, inleder en ny epok av ”robotmedarbetare” som kan utföra samma arbetsuppgifter som människor, sida vid sida på ett monteringsband med garanterad personsäkerhet.
2015-04-13 – ABB, det ledande kraft- och automationsföretaget, presenterade idag YuMi, världens första i sann mening samarbetande tvåarmade industrirobot, vid världens ledande industrimässa i Hannover.
Lanseringen av YuMi är ännu ett steg i ABB:s strategi Next Level som syftar till att accelerera hållbart värdeskapande. Strategin bygger på ABB:s tre fokusområden lönsam tillväxt, kraftfullt genomförande och affärsdrivet samarbete. Lönsam tillväxt ska uppnås genom att flytta företagets tyngdpunkt mot snabbväxande slutmarknader, öka konkurrenskraften och minska risken i affärsmodellerna.
”Den nya epoken av robotmedarbetare är här, och är en inbyggd del av vår strategi Next Level”, säger Ulrich Spiesshofer, koncernchef för ABB. ”YuMi gör samarbete mellan människa och robot till en realitet. YuMi är ett resultat av flera års forskning och utveckling som kommer att förändra synen på hur människa och robot kan arbeta tillsammans. Den är en del av vår strategi för Sakernas, tjänsternas och människornas Internet för att skapa en automatiserad framtid tillsammans.”
År 1974 lanserade ABB världens första mikroprocessorstyrda, helektriska industrirobot, vilket gav en kickstart för den moderna robotrevolutionen. Med lanseringen av YuMi flyttar ABB återigen gränserna för robotautomation genom att fundamentalt utöka antalet automatiserbara industriprocesser.
Få produktionsprocesser är under så snabb förändring som monteringen av små komponenter. Speciellt elektronikindustrin har sett en tillväxt av efterfrågningar som vida överstiger tillgången på utbildad arbetskraft. Eftersom konventionella monteringsmetoder minskar i värde är det strategiskt och ekonomiskt motiverat för tillverkare att investera i nya lösningar.
Till exempel förutspår prognosföretaget BCG Research att till år 2025 kommer användningen av avancerade robotar att ha höjt produktiviteten med upp till 30 procent i många industrier och sänkt totala arbetskraftskostnaden med 18 procent i flera länder, såsom Sydkorea, Kina, USA, Japan och Tyskland.
YuMi är specifikt designad för att tillgodose kraven på flexibilitet och snabb omställning i produktionen av konsumentelektronik men den är lika tillämplig för andra typer av småkomponentsmontering. Detta tack vare robotens två armar, flexibla händer, universella matningssystem, kamerabaserad komponentplacering, lead-through-programmering och avancerad, exakt rörelsekontroll.
YuMi kan arbeta i nära samarbete med människor tack vare den inbyggda säkerheten i robotens grundkonstruktion. Den har ett lättviktigt och ändå starkt magnesiumskelett täckt med formgjuten plast som vadderats med mjukt, stötabsorberande material. Den är också kompakt, med mänskliga dimensioner och ett mänskligt rörelsemönster, vilket gör att de som arbetar sida vid sida med roboten känner sig trygga och bekväma. Dessa egenskaper har gett YuMi utmärkelsen ”Red Dot ‘best of the best’ design award.”
Om YuMi känner av en oväntad beröring såsom en sammanstötning med en medarbetare kan den stoppa sina rörelser på en millisekund. Att sedan starta upp den igen är lika enkelt som att trycka på play på en fjärrkontroll. YuMi har heller inga klämpunkter som innebär risk för klämskador när axeln öppnar och stänger sig.
ABB (www.abb.com) är ledande inom kraft- och automationsteknik. Våra lösningar förbättrar prestanda och minimerar miljöpåverkan för kunder inom energi, industri, transport och infrastruktur. ABB-koncernens bolag verkar i omkring 100 länder och har ungefär 140 000 medarbetare.
Länk till bild
Länk till b-roll
Länk till infographic
Länk till YuMi page
YuMi background information and further details:
In 2006, the world was at the very beginning of the smartphone revolution. At the time we could only imagine how this market would develop. Many envisioned a future that would bring exploding demand for affordable, miniaturized, mobile electronics.
That is why nearly a decade ago we began re-examining our approach to robotics and automation, in general. In particular, we focused on replacing complex and complicated processes with flexible and agile systems. In time, these advancements collectively came to be known as the Integrated Industry or the so-called fourth industrial revolution. Cyber-physical systems, production scenarios and real man-machine-collaboration are the keys to successfully managing the ecosystem of people, things and services growing out of this revolution. In addition this new kind of collaboration has to deliver balanced solutions able to utilize this ecosystem’s greatest strengths in a sustainable, efficient and profitable way.
Today, the market has turned into something beyond our wildest expectations. It is more complex than we ever imagined and requires an incomprehensibly vast system of manual assembly. Millions of workers, across thousands of assembly lines, build the electronics upon which the world has come to depend. The explosive growth and extremely short life cycles of these types of products, coupled with rising demand for more rewarding jobs, higher pay and better quality of life among workers, means that, ultimately, the current system is neither scalable nor sustainable.
Looking back to 2006, when we started developing the concepts for a small parts assembly solution that addressed these issues, we did not know just how great the need would be. We understood that these manual assembly lines would have to be automated—and that it would be a transition that would likely take decades and would need to happen without disruption to the complex, vast and deeply ingrained existing small parts assembly infrastructure. As such, whatever solution we developed would have to be robotic in nature, and it would have to work safely next to humans. These days we call this concept human-robot collaboration, but back then we were simply thinking of it as creating an inherently safe solution.
We knew that this market required the flexibility to handle constantly changing products that have life cycles on the order of several months and shrinking. The solution needed to be easily portable and re-deployable as well as able to fit into existing workspaces designed for humans. It also needed to employ innovative programming methods so intuitive to use anyone can do it without special training. It had to have senses and motor control comparable to humans. Above all, though, it needed to be safe enough to work side-by-side with its human coworkers without safety caging and without being threatening.
That vision is what ultimately led to YuMi.
YuMi: Creating an automated future together
With the introduction of YuMi, the world’s first truly collaborative dual-arm industrial robot, ABB Robotics is once again pushing the boundaries of what robotic automation will look like in the future and how it will fundamentally alter the types of industrial processes that can be automated with robots.
A play on words, YuMi signifies “you” and “me” creating an automated future together. This groundbreaking solution is the result of years of research and development, heralding a new era of robotic coworkers that are able to work side-by-side on the same tasks as humans while still ensuring the safety of those around it.
Few production arenas are changing as quickly as small parts assembly. The electronics industry, in particular, has seen demand skyrocket past the supply of skilled labor. As conventional assembly methods diminish in value, manufacturers are finding it strategically and economically imperative to invest in new solutions.
While YuMi was specifically designed to meet the flexible and agile production needs required in the consumer electronics industry, it has equal application in any small parts assembly environment thanks to its dual arms, flexible hands, universal parts feeding system, camera-based part location, lead-through programming, and state-of-the-art precise motion control.
At first glance, processes on manual assembly lines might seem relatively simple to automate, but in reality it is not so easy to replicate human abilities—we are amazing machines. We have touch and motor control which allows us to handle delicate things with dexterity and precision, as well as judge how much force to use on a given component so that we do not break it. We can see where an item is, easily pick it up, and are able to handle an incredibly diverse variety of parts without pausing. We also have spatial awareness which allows us to interact closely and in harmony with our coworkers.
With YuMi, the challenge was to determine how to replicate all of these human attributes in a way that was cost-effective—essentially recreating the minimum number of senses and abilities necessary to be at least as safe as humans, yet still able to provide the substantial benefits of automation. Through purpose-built design that is much more than just the robot, we have created an inherently safe system of components that delivers the precision, ease-of-use, speed, flexibility and return-on-investment required for the future of small parts assembly.
At its core, YuMi has the DNA of safety. Much like a human arm has a skeleton covered with muscles that provide padding, YuMi has a lightweight yet rigid magnesium skeleton covered with a floating plastic casing wrapped in soft padding. This arrangement absorbs the force of any unexpected impacts to a very high degree. Like the human arm, YuMi has no pinch points so that sensitive ancillary parts cannot be crushed between two opposing surfaces as the axes open and close.
YuMi is compact, with dimensions similar to that of a human, and dual-arms featuring seven axes of movement each allow the robot to have great dexterity and precision inside a compact, human-sized workspace. YuMi only weighs 38 kg, has an integrated control system, integrated internal cabling for a multitude of input and output commands including air and digital, works off of standard household electrical power found the world over, and is extremely portable and re-deployable at will.
If YuMi senses an unexpected impact, such as a collision with a coworker, it can pause its motion within milliseconds, and the motion can be restarted again as easily as pressing play on a remote control. When this is combined with the floating padding, safety for a human coworker is drastically increased. Even with these inherent safety features, YuMi is incredibly precise and fast, returning to the same point in space over and over again to within 0.02 mm accuracy and moving at a maximum velocity of 1,500 mm/sec.
To handle the great variety of parts that are seen in today’s small parts assembly environments, YuMi comes with integrated and highly flexible hands which can be deployed in a variety of configurations, including servo grippers, dual suction cups, and vision. Altogether, YuMi’s hands allow for complete customization to meet the demands of most assembly tasks.
However, the complex operational problems found in small parts assembly do not simply revolve around the flexibility of human hands; supplying the parts for a given task is also key to efficient operation. To address this we developed the FlexFeeder™ system for parts delivery. The FlexFeeder stores a large number of parts, ranging from 3 mm to 30 mm in size, in a bin. Picking parts directly from the bin is a very complicated three-dimensional problem, so the FlexFeeder turns this into a much easier two-dimensional picking operation by serving those parts from the bin in small numbers up onto a flat surface. From this flat surface YuMi’s integrated hand cameras can easily locate and then direct the grippers to pick parts.
Finally, to make programming YuMi as simple as telling a human what to do, we have created a programming system so easy anyone can use it. In fact, we hesitate to even call it programming. It is more like teaching—and everyone intuitively knows how to teach. Simply guide YuMi’s arms and hands, using your own arms and hands, through a series of movements, logging waypoints and gripper actions on a paired tablet running the YuMi app. Watch as the software turns those movements into the underlying code that makes YuMi work—right in front of your eyes and in real-time. This means that YuMi requires far fewer engineering resources to accomplish very complicated tasks.
Lead-Through Programming can turn what used to be hours of tedious programming into a few minutes of easy work. When the tasks are more complicated than Lead-Through Programming allows, full access to traditional coding using ABB’s RAPID programming language is still there when you need it.
Why YuMi is important to the world
If we take all the features and innovations encompassed in this product, we are not just providing a robot, we are providing a complete solution for the automation of small parts assembly. For the manufacturers who employ YuMi, the benefits will be undeniable in terms of faster production, higher quality products, lower waste, greater efficiency, increased flexibility and incredible return on investment—but YuMi is much more than an economic growth stimulator.
If we analyze YuMi through the lens of ABB’s vision of “Power and Productivity for a Better World,” YuMi clearly addresses the productivity portion. It also helps create a better world by providing a strong means to decouple economic growth from both environmental and human impact.
As a complete solution, YuMi not only benefits the manufacturer, it benefits the entire value chain, from the manufacturer to the worker, to the environment, to the consumer of the product. It is better for the worker because it provides a safer working environment and a higher quality of life. It is better for the environment because it has lower inputs and results in less waste. Ultimately, it is better for the consumer because when humans and robots work together, it often results in surpassing the precision and speed of human-only work, resulting in higher quality products and less waste.
Benefits of human-robot collaboration into the future
While YuMi is specifically designed for small parts assembly, and has significant benefits in its own right, it is only the first solution from ABB designed with a new era of human-robot collaboration in mind. The benefits of collaboration clearly are not limited to a single industry; in fact, almost any industry stands to reap the benefits of collaborative robotic solutions.
Firstly, collaboration allows for the automation of processes which still require humans to be part of the solution and cannot be fully automated with existing technology. This opens up entirely new and untapped markets to automation.
Secondly, while conventional robotic systems will still be needed for a long time to come and have several key advantages over current collaborative technology (e.g. higher payloads, much faster cycle times and stronger protection from harsh environments such as foundries), collaborative robots are far less resource-intensive in terms of system design, installation, commissioning and operation when compared to conventional industrial robots. In fact, many conventional robotic systems have already realized some of these benefits thanks to advances in software and hardware safety control, like ABB’s SafeMove technology combined with different kinds of vision and environmental monitoring systems making them “partially” collaborative.
In particular, fully collaborative automation without safety restrictions and in compact spaces makes for easier factory installation utilizing existing footprints. Programming in the collaborative environment can also be done by “teaching” the robot rather than using a coding language. While system operators can always use ABB’s powerful underlying RAPID programming language if they choose, the ability to interact with the robot while moving it around and training it how to get from point A to point B means that many new tasks can be trained in a matter of minutes as opposed to hours. Altogether, ABB’s collaboration system of components, including the robot, makes for much simpler integration of robotic automation.
Thirdly, collaborative robots elevate the nature of work by allowing people to do the jobs that require more thought and are less physically demanding. In addition, when humans and robots work together, it often results in surpassing the precision and speed of human-only work, resulting in higher quality products and less waste.
As demographics change around the world, and standards of living across the planet rise, people will increasingly seek the jobs that are more mentally rewarding. To keep up with this change, collaborative robots simultaneously make workplaces more appealing and replace the manufacturing skills that are disappearing from the workforce.
Robots and jobs
As the robotics market continues to exhibit explosive growth, collaborative human-robot workplaces will be a large driver of that growth, thanks to increased ease of deployment and operation, as well as the automation of many industries that were previously considered impossible to automate effectively.
The topic of how this increase in robots in the workforce will affect jobs is one that has captured much attention. ABB believes in a more optimistic outcome from the increasing adoption of robots and the explosion in automation as a result of the increase in human-robot collaboration and the convergence of other technologies. This optimism is not borne out of a sense of idealism, but is instead rooted in the experiences conveyed to us by history.
Every single major advance in over the past few hundred years of industrialization has resulted in a stronger economy, not a weaker one. It is true that after each of these advances, some types of jobs have become unnecessary. However, many more jobs have been created as a result of the advances, so the job loss is only restricted to the areas that were made obsolete and the overall effect has been that of job growth—most significantly in areas that no one could have imagined before the invention of the technology that allowed for those jobs.
The freeing up of humans from the drudgery of tasks that should be automated will likely result in a new kind of economy that is focused on harnessing human creativity instead of human productivity. It is not that robots are taking humans’ jobs, it is that humans were doing the jobs robots should have been doing for first few hundred years of industrialization—and now the technology of automation has finally caught up to allow robots to do the jobs they are best suited for.
Certainly, the economy of the future will be drastically different from the economy of the first few hundred years of industrialized society. We do not know what that future will look like, but if history is a lesson, it will likely be full of jobs that are better suited to humans and do not cause the kinds of workplace injuries, both physical and mental, that can exist in today’s manufacturing environments. At ABB, we would not be pursuing this kind of technology if we did not believe it will result in a better world for all human beings.
Conclusion
With the rise of collaborative robots we will see a drastic change in the way manufacturing is automated and conducted in the future. We will also see a paradigm shift in the way humans do work and what types of work are considered valuable.
Just like every other major advance in the history of industrialization, the increasing automation of more and more jobs will result in an explosion of newer and better jobs, some of which we cannot even envision right now. ABB is dedicated to making the world a better place, and collaborative robots are going to be a strong part of that.
With the era of collaborative robots we recognize the fact that humans and robots both have their own strengths, and when working together, shoulder-to-shoulder, in a safe manner, the workplaces of the future will be more flexible, produce better quality products with fewer resources, provide a safer working environment, improve employee quality of life, and make companies
För mer information, kontakta:
ABB Group Media Relations:
Thomas Schmidt; Antonio Ligi, Sandra Wiesner
Switzerland: Tel. 41 43 317 6568
media.relations@ch.abb.com
Taggar: