Full Steam Ahead for the Museum 'Marhsall'
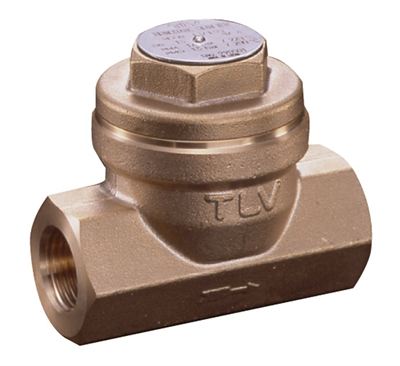
The Museum of Power near Maldon, Essex is housed in a newly refurbished, former water pumping station and contains a fascinating collection ranging from a working Edwardian overhead machine shop to a diesel powered iron and a miniature railway. However, the highlight of the museum’s collection is ‘Marshall’, a 300hp vertical triple-expansion reciprocating steam engine manufactured by the Lilleshall Company which, thanks to design advice and the supply of hotwell equipment and steam traps from TLV Euro Engineering, is now back on steam after nearly 50 years.
The steam engine dates back to the 1930s when it was used to pump water from the local reservoir to the water treatment works. Once treated, the water was then pumped to Southend via a 24 inch water main at a capacity of between 4 and 4.4 million gallons per day. Marshall is the sole-survivor of three engines and pumps originally housed at the station. The other two were removed for scrap when they were turned off in 1963 and the site was eventually decommissioned by Southend Waterworks in 1965. Today, the engine still powers the high- and low-pressure pumps, but does not actively pump water.
Having secured a deal with Essex & Suffolk Water, The Museum of Power took ownership of the premises and Marshall in 1996 and completely refurbished the steam engine. As the charity had limited funding the engine was only re-commissioned to run on compressed air. However, following years of fund raising, and with grants received from the local council and Essex & Suffolk Water, the museum had raised enough money to re-engineer the engine to work on both steam and compressed air.
Commenting on the re-commissioning, site engineer John Stopps says the museum managed to secure a 30 year old steam boiler from Felixstowe Docks. This was refurbished and installed in a new plant room which, thanks to help from TLV Euro Engineering, was equipped with all the services required to power the steam engine.
Adds John: “The museum is lucky enough to have volunteers that have worked as ships engineers, so with help from TLV we were able to design the pipework ourselves. Not only was TLV kind enough to offer their help free of charge, they even supplied the required hotwell equipment and steam traps at cost, which saved the museum a significant amount of money.”
The equipment supplied by TLV Euro Engineering includes its cast stainless steel J3S-X free-float steam traps, which can be installed on various types of equipment that use steam as a heat source; and provides continuous, smooth, low-velocity condensate discharge as loads vary. The patented design also only features a single moving part – the free float – which prevents concentrated wear and provides a long, maintenance-free life. In addition to its compact size and large condensate discharge capacities, the J3S-X steam traps are also equipped with an X-element air-vent to provide a powerful, automatic air vent function.
Also supplied were TLV’s patented, brass-bodied LV13N balanced pressure thermostatic steam traps, which feature a ‘fail-open’ design, are operated by the temperature difference between the steam and condensate and incorporate a multi-diaphragm construction for long service life.
Explaining the reasons for converting the engine back to steam, John Stopps says it was always the museum’s intention to have the engine working on steam, but timing and funding prevented them from doing it. “It was and still is a steam engine,” he says: “so why not have it powered by steam. It’s a real pleasure to see it working again!”
Following its re-commissioning, Marshall was first ‘steamed-up’ in April 2011 and has been operated a further six times since. The Museum of Power plans another six steam-powered displays for the 2012 season, the first of which took place on Easter Sunday.
The Museum of Power can be found in Langford, near Maldon in Essex. For further information email enquiries@museumofpower.org.uk, call 01621 843183 or visit www.museumofpower.org.uk.
Ends
For further information contact:
Michael Povey, TLV Euro Engineering UK Limited
Star Lodge, Montpellier Drive, Cheltenham, Gloucestershire, GL50 1TY
Phone: 44 (0)1242 227223, Fax: 44 (0)1242 223077, Email: michaelpovey@tlv.co.uk, Web: www.tlv.com
For press information contact:
Simon Cantillion, Cantillion King Advertising 16 The Cornhill, Stroud, Gloucestershire, GL5 2JT
Phone: 44 (0)1453 755551, Fax: 44 (0)1453 751525, Email: simon@cka.co.uk, Web: www.cka.co.uk
About TLV Euro Engineering:
TLV Euro Engineering was founded 60 years ago and is a recognised global leader in steam engineering. The company offers a wide range of steam engineering products supported by services including consulting, site inspections and seminar training.
TLV has always strived to manufacture innovative, high-quality, long-lasting products and systems and one of its early successes – the A3 steam trap – was awarded no less than seven patents. This steam heating, condensate cooling, double jacketed thermodynamic steam trap is unaffected by ambient conditions and offers an incredible 10 times the durability of previous products.
TLV designs and manufactures a range of products and systems such as the award-winning CV-COS, an electro-pneumatic pressure reducing valve with a convenient control function; and the Vacuumizer, a vacuum pressure steam heating and cooling system. TLV has also revolutionised fluid control technology with the launch of its patented ‘Free Float’ steam traps which, with only one moving part, guarantee long life and reliability.
Tags: