Faster printing for the next generation of SLS printers from Wematter
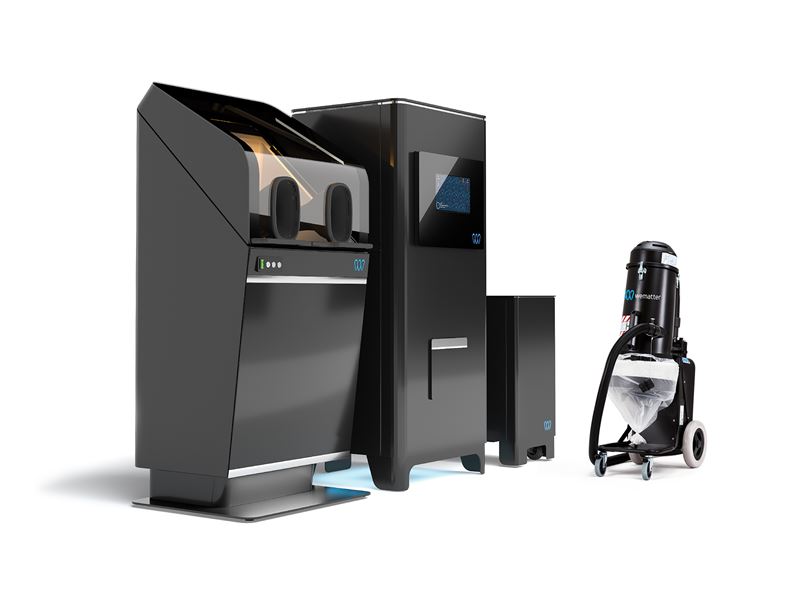
At Formnext 2022, the Swedish manufacturer of SLS 3D printers Wematter launches a new version of the Gravity SLS 3D printing system. It is a complete system for speeding up R&D processes at companies with several R&D and technology development centers. It will support integration between geographically dispersed teams, facilitate a quicker and fuller understanding of ideas and concepts across countries and continents, and will typically cut development times by three quarters.
The Wematter SLS 3D printing system includes five parts, integrated into clever ways to enable easy handling. It is as easy to handle and install as a copier machine or a domestic fridge. The whole system can be brought through a domestic door and be kept in a relatively small room.
- Gravity SLS 3D printer. As of Formnext, the upgraded and improved 2023 version can print well over 20 different materials. It is equipped with a high-power (50 W) CO2 laser combined with a high-speed laser scanning assembly. Through new components and algorithms, the scanning speed has been increased by 2 times compared to last year's model. A 200% increase in top speed saves up to 15 hours on a typical print job boosting productivity significantly.
- Density water-jet cleaning cabinet, used for depowdering of 3D-printed parts. This year, Density has undergone a lot of design changes with a focus on productivity. With these enhancements and a new variable nozzle, this year's model is the fastest and cleanest solution for SLS printing on the market. The core of Density is that it uses high-pressure water without the need for plumbing or water connection.
- The Deep Space software tailored specifically for Gravity automates the workflow to a large extent. Preparing the build becomes a quick and rewarding exercise, finished in no time. Anyone in the organization will learn Deep Space in an hour. Engineers and product developers will have even more fun developing new components. The focus of the 2023 upgrade is on user experience and many new algorithms and solutions under the hood will create a fluent and swift process from import to print.
- Atmosphere ensures a stable atmosphere in the build chamber of Gravity. This unit is key to print quality. It is delivered as a separate unit to simplify transportation and placement of the system and service.
- Inertia, effective and easy-to-use powder collector used to vacuum most powder from the Gravity build volume after finished print, before the printed parts are moved to Density for cleaning. This ensures minimum powder spillage and a more ergonomic workflow.
New polymer material for SLS 3D printing
Just as important as the system itself are the materials it can print. As part of Wematter’s strategy, the material portfolio is once again expanding. A special focus is on food-grade components and for that application, the biggest news is Aurora PA11 Food Grade – a blue polymer which is approved for contact with food. The blue color makes it easy to spot broken parts that could fall into the food during production.
“With the Gravity 2023 system, we now have the most competitive offer for any R&D department that has people working in different locations”, says Robert Kniola, founder and CEO at Wematter.
If you are planning to visit the Formnext 2022 exhibition, please drop by the Wematter booth B69 in hall 11.1 and see all our polymer materials and the Gravity 2023 SLS 3D printing system.
For more information, please contact:
Daniel Delviken
Marketing Director
+46 (0)739 65 80 32
press@wematter.se
About Wematter AB (publ)
Swedish 3D printing company Wematter's pioneering solution gives hospitals, offices, and workshops access to a comprehensive system. For the first time, employees can easily print components themselves with the same strength and quality as traditional technology. Wematter’s proprietary end-to-end solution enables customers to accelerate product development and in-house volume production. At the same time, the system creates the conditions for increased flexibility, lower risk and reduced manufacturing and development costs. For more information about Wematter, visit wematter3d.com
Tags: