Inline washing for stampings with high purity requirements
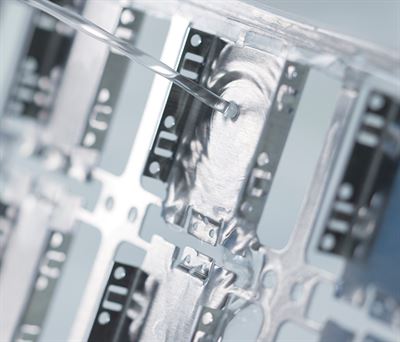
Velleuer, part of the Lesjöfors Group, has developed a manufacturing process for stampings with extreme purity requirements for the German automotive industry. In custom-built washing equipment the components are cleaned, rinsed and dried.
The German spring manufacturer Velleuer has been a part of the Lesjöfors Group since 2011 and has successfully been a well-respected partner to the automotive industry for decades producing technical springs, stampings and pressings. Two years ago, a project was launched with a leading automotive supplier, where the end product is a stamped aluminum tray with very high standards for precision and purity.
Purification of exhaust gases
The product is used for motor control in combustion engines to meet the highest demands on purification of exhaust gases. The development process took 15 months before the idea turned into a product. By an especially designed inline washing machine the components are cleaned, rinsed and dried and then coiled onto a reel for quality controls and storage of the products before delivery.
High quality demands and frequent controls
Quality is an essential aspect in every step of the process to ensure the highest customer satisfaction. To ensure the quality level of the product tests were frequently carried out, both by Velleuer staff as well as customer representatives. The component is produced as a couple in a progressive stamping tool, connected to the grid where a multi-step washing process cleans the product and wraps it with a lint-free intermediate layer.
“When the production process was designed, it was essential to prevent the formation of metal chips and scratches. All appliances, machinery and contact areas have been reviewed to optimize cleanliness. The less chips and particles there are, the less has to be washed off, since everything is embodied in the process”, says Thomas Woltring, production manager for strip components at Velleuer.
In the custom-built test lab, equipment is provided for continuous monitoring and improvement opportunities. The environment is created to detect particle sizes smaller than 200 μm and is largely automated in order to achieve reproducible results.
Specialized development partner for high purity products
The process development is based on the new standard for the German automotive industry VDA No. 19. Today, Velleuer is regarded as one of the most qualified suppliers in the development of components with extreme purity requirements.
“We see a rapidly growing interest in the production of the highest cleanliness requirements from many of our customers from diverse industries, so we know our thinking is right in time. The brand Velleuer is a quality mark of both products and our solution-oriented approach”, says Axel Bitzer, sales technician at Velleuer.
For more information, please contact Velleuer GmbH & Co. KG.
Tags: